SSM Textile Machinery, a manufacturer of winding machines within the Rieter Group, offers an advantageous air covering method for dual-core spinning. Items of clothing such as jeans were produced purely from cotton in the past, however, elastic woven fabrics became established in the clothing industry thanks to their positive characteristics for some time now. So-called corespun yarns with a dual-core that are spun on a ring spinning machine are used for weft threads and sometimes also warp threads to produce these elastic yarns. Traditional ring spinning mills are upgrading their machines in order to compete in this market due to the increased demand for elastic yarns. SSM offers an efficient solution to traditional ring spinners with the XENO-AC TWIN method, an opportunity to enter the elastic corespun yarn market and achieve success. This user-friendly and safe method also allows production with no compromises on yarn quality.
Corespun yarns that are used to produce woven stretch fabrics consist of an elastic core with a second spinnable fibre wrapped around its entire length. The core can only be made from elastane, or alternatively, from an elastane yarn and a textured filament yarn known as ‘dual-core yarn’. In addition, a trend for making the core from two elastane yarns with different drafts and yarn counts together with a textured filament yarn is observed. These ‘triple-core yarns’ further improve the characteristics of these woven stretch fabrics in terms of their stretch and shape-retaining characteristics.
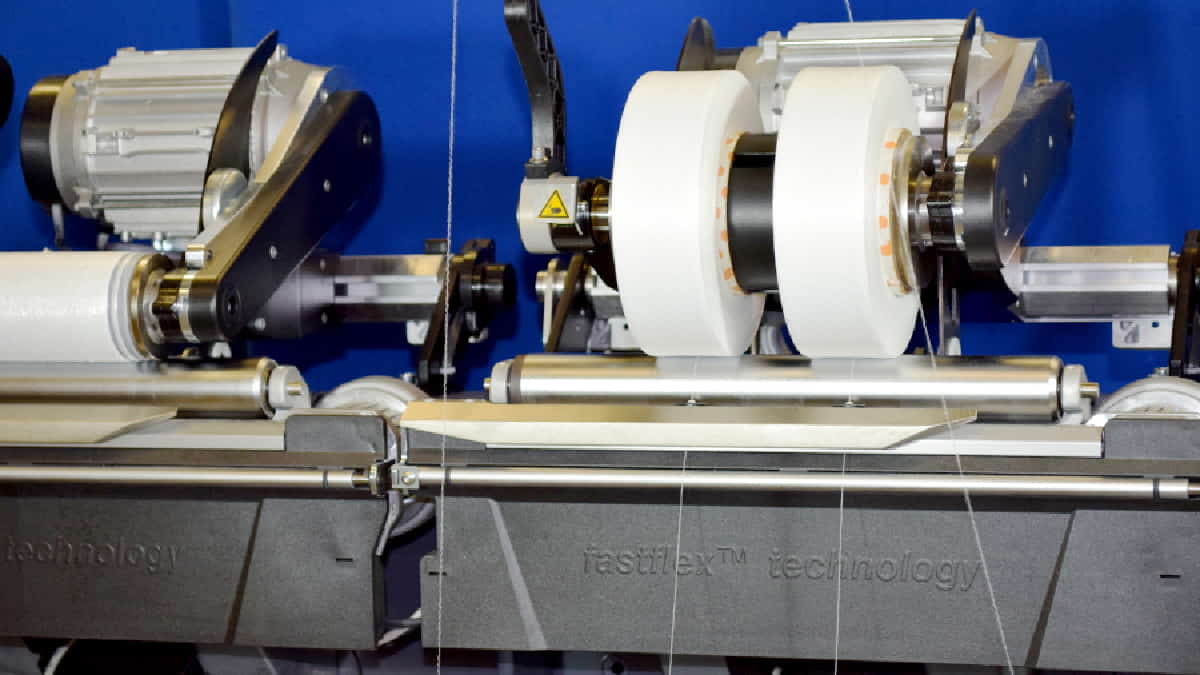
Two production possibilities for dual-core yarn production
There are essentially two methods of producing corespun yarns with a dual or triple core. The elastane yarn and textured filament yarn are spun directly on a Rieter ring spinning machine with the spinnable fibres that act as sheathing in the first method. In the second method, the elastane yarn and textured filament yarn are doubled, air-covered and wound up together on a XENO-AC TWIN machine before being processed on the ring-spinning machine. In a second step, cotton is spun over the dual- or triple-core yarn located on the ‘cheese packages’, for example using a Rieter ring spinning machine. Both methods require specialized superstructural parts to be fitted on existing ring spinning machines.
These superstructural parts are very tall for the direct method in which the dual- or triple-core yarn is not pre-wound and must be switched off in order to reload the ring-spinning machine. This method causes a productivity loss of around 13% in comparison to the indirect method and furthermore, the operating personnel have to climb onto the ring-spinning machine in order to place the bobbins with the textured filament. This is not only dangerous but also means that additional personnel are temporarily required who could be utilized for other operational tasks.
Non-stop production with the indirect method
Producing corespun yarns with a dual- or triple-core using the indirect method requires an additional work step: preparing the core yarn using the air covering machine XENO-AC TWIN. The bobbin holder on the ring-spinning machine needed for this solution provides a much lower and more user-friendly process. A further advantage is that each spinning position can be loaded while all the other positions continue to operate and this means there is no production downtime while the machine is being reloaded. It is stated that the conversion costs for both methods are approximately the same, however, the XENO-AC TWIN method might be slightly cheaper.
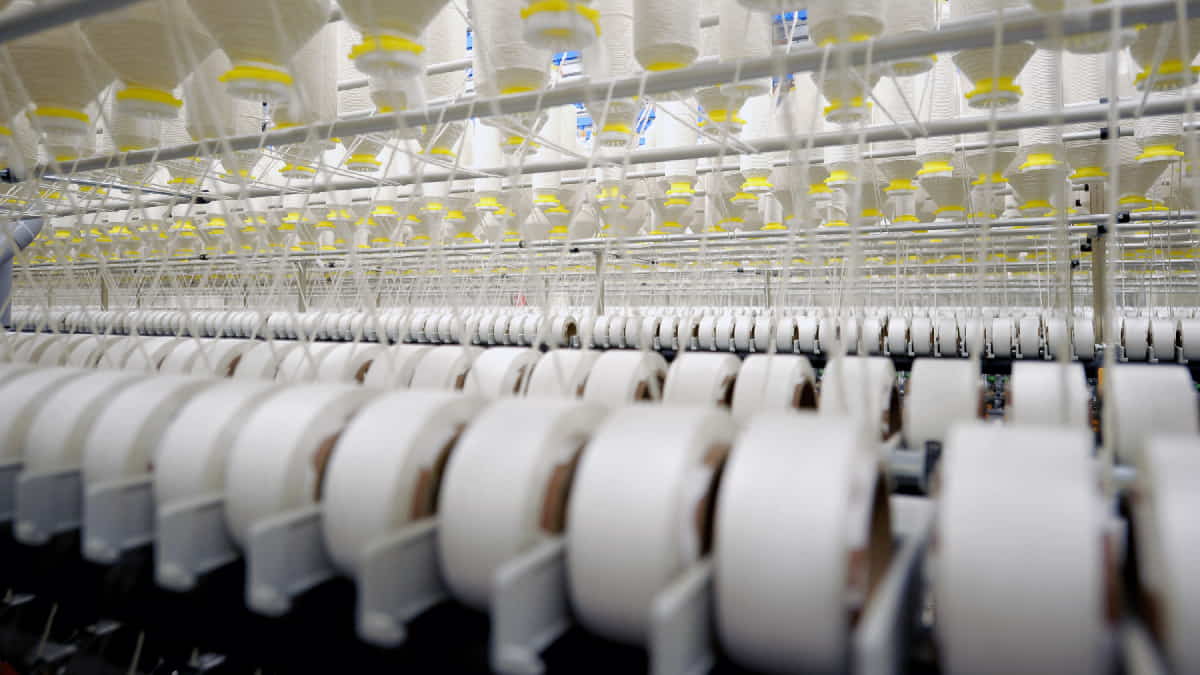
Air covering machine ensures consistent quality
The main advantage of the ‘indirect’ method with the air covering machine is that the core yarn is centred better during processing on the ring spinning machine and is very well covered with the spinning staple fibres as a result. This ensures that the core yarn is optimally protected. While it is very difficult for the operator to detect a non-centred core yarn in the yarn, this flaw can only be seen once the fabric has been woven and dyed. Poor centring of the core yarn can create flawed spots in the woven fabric that disrupt its overall appearance since elastane cannot be dyed. The air covering machine ensures consistent quality and consequently reduces complaints. Corespun yarns with a dual- or triple-core where the filament has already been doubled and air-covered on an air covering machine, therefore, offer a higher quality than corespun yarns produced directly on a ring spinning machine.