In the global textile and fashion industry, the demand for yarns and fabrics with shiny and fancy effects is constantly increasing. SSM, the spinning solutions specialist, which has a 300-year tradition and has been working as a subsidiary of Rieter since 2017, offers creative new solutions in this regard.
Metallic-coated yarns such as Lurex have been well established in the market for decades. One current trend is to integrate these yarns into fabrics to achieve a shiny and fancy effect. Featuring specific yarn combinations, these yarns are finding a wide range of applications, from home textiles to fashion apparel including shoes and hosiery.
The market is constantly in search of unique fancy products. With this in mind, SSM has worked to develop an innovative way of creating brand-new combinations using the air-covering process. The SSM XENO-AC produces not only standard air-covered yarns, but also sophisticated yarns in which Lurex is added to various filament yarns such as PES and PA, either DTY or FDY. These yarns give the final knitted or woven fabric an exceptional shiny effect with incomparable properties. The production process involves Lurex thread being inserted into an air-pressure nozzle along with one or more filament yarns where they are then comingled. Figures 1, 2 and 3 show the special yarn path that has been engineered to achieve a smooth and regular feed of the metallic-coated thread directly from the supply packages.
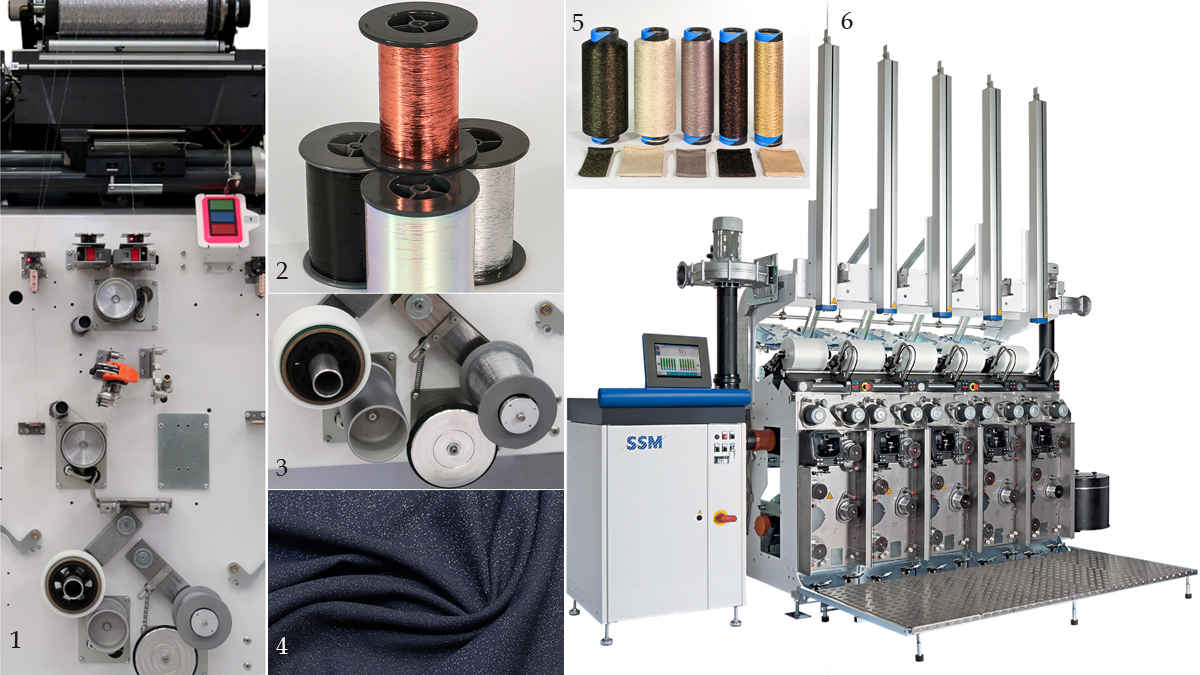
Filament Lurex covering
The filament yarn covering the Lurex reduces itchiness; and lends the fabric a softer touch than that achieved through direct use in knitting or weaving. The filament cover also protects the Lurex from abrasion and prevents breakage in downstream processes. For some products, the air-covering process can replace more expensive and slower conventional covering processes; used to cover filaments with Lurex. Typical production speed for the air-covering process of Lurex is about 20 times higher than conventional covering. Furthermore, elastane can be fed into the yarn, enhancing the fabric properties; by creating a stretch effect for glittery and elastic fabrics commonly used in denim, socks, and hosiery. Figure 4 shows a woven fabric and figure 5 various yarn packages; with fabric samples made of filament yarn and Lurex.
A retrofit is available for customers who already own a XENO-AC; and can easily modify a standard execution to handle Lurex. A similar retrofit is also available for the SSM DP5-T air-texturing machine (Fig. 6), in turn providing manufacturers even greater flexibility in the creation of new types of fancy yarns.