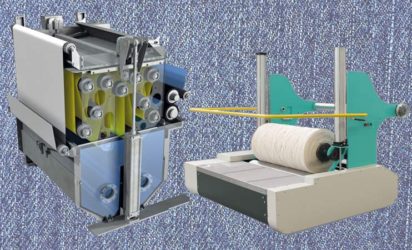
KARL MAYER launches the PRODYE-R – a customised dyeing machine for the rope dyeing process.
Jeans are the perennial evergreens of the clothing sector. Their characteristics and looks change all the time, so that they are always on trend. The different appearances are created by different production techniques – particularly by the dyeing processes involved.
Whereas fabrics for fashion denim are normally dyed by the slasher-dyeing process, fabrics that are used for producing classic American blue jeans are dyed using the rope dyeing process.
KARL MAYER can supply the most suitable dyeing technology for both processes in the shape of its PRODYE system, which has already become very well established on the market. As far as slasher-dyeing technology is concerned, this well-known company leads the market in the fashion denim sector. In the last three years, KARL MAYER has delivered eight machines only to Turkey. For some time now, the company has been working hard on developing new rope dyeing applications, especially in this traditional denim-producing country.
Technological advantages of the slasher-dyeing line for the rope dyeing process
The PRODYE-R technology combines the technical achievements of three years of development work at KARL MAYER, and delivers maximum performance during indigo dyeing. Compared to similar systems available on the market, this innovative technology reduces water consumption by roughly 30% in practice, decreases yarn wastage, and produces deeper indigo shades during the slasher-dyeing process. What is more, the productivity is almost twice as high when processing lightweight denim. With this type of product, customers can achieve an output of up to 70 m/min.
This unique performance is the result of a number of technical features, including the Double Vario dyeing unit. This application system is the key element of the PRODYE system. Its optimised flow patterns and efficiency result in flexible and process-specific immersion lengths and times during pretreatment and dyeing. The technical features of the Double Vario include a well-thought-out cross-flow system for perfect dyebath circulation and an integrated system for raising the immersion rollers. The latter simplifies handing, minimises cleaning times and guarantees stable liquor baths during machine downtimes.
An integrated, indirect heating system also enables a range of dyeing techniques, such as reactive, sulphur and indanthrene dyeing, to be carried out reliability and flexibly. Finally, squeeze roller pairs operating at 100 kN, which are harmonised with each other, at the end of the processing sequence in the dyeing machine guarantee uniform fabric transport and avoid variations in the circumferential speed at the textile material. The design of the Double Vario has been optimised to enable it to be integrated into the PRODYE-R rope dyeing system.
Complete solutions for the rope dyeing process
As well as the actual dyeing technology; KARL MAYER can also supply all the other machines and equipment needed for rope dyeing. The full one-stop package consists of various creels; the BALL WARPER, the LONG CHAIN BEAMER and the PROSIZE® sizing machine.
The BALL WARPER forms the ropes for producing beams having a maximum diameter of 1,500 mm; and operates in a controlled, tension-regulated, gentle and precise way. The technical features that are responsible for improving performance include; for example, pneumatically controlled disc brake technology for synchronous braking; and an integrated suction system for removing fly and other contaminants. Removing these impurities reduces contamination during wet treatment.
The LONG CHAIN BEAMER produces beams having a maximum diameter of 1,000 mm. A pneumatically operated, self-centring, toothed, sharply tapered beam mounting; and an infinitely adjustable presser roller device, including an automatic kick-back facility; guarantee reliable processing and easy handling. The latter guarantees perfectly cylindrical beam winding. An integrated, reverse-driven compensator also enables the operating status during rope feeding to be changed at constant rope tension levels.
The PROSIZE® sizing machine operates with the new VSB Size Box; and the sizing result guarantees first-rate efficiency during weaving. Its advantages include compact yarn feed, short yarn paths, accurate process control, and a high level of reproducibility. The PROSIZE® is also easy to operate.