UK-based 3D weaving machine manufacturer Optima 3D has developed the next generation Optima 500 Series 3D weaving machines for the composite industry. The Series 500 range offers many advanced features over conventional offerings particularly in versatility, operation and control. This has been achieved by the comprehensive use of digital control systems allowing rapid parameter and sequence changes coupled with an innovative shuttle system. Prototype machine trials including field testing have now been completed; and the first production machine, an Optima 500/150/1; is in the final stages of commissioning prior to its public debut at ITMA 2019, Barcelona.
Optima 3D machines feature innovative technology, and offer versatility, capable of producing high quality woven net shapes, billets & para beams for composite applications. Interest has been received from a number of engineering sectors including aerospace, military, bio-medical and automotive.
Powered & controlled by cutting edge digital technology, each machine allows automatic control plus touch screen management of all machine settings also enabling pattern and machine data to be stored and printed, vital for industry accreditation regarding quality assurance and safety regulations.
The Optima approach allows users a greater flexibility in their component design than ever before, making the Series 500 suitable for both production and R&D purposes. The compact Optima design allows a complete 3D weaving system to be easily installed; equally, it’s extremely competitive price now makes a complete R&D 3D weaving system significantly more attainable.
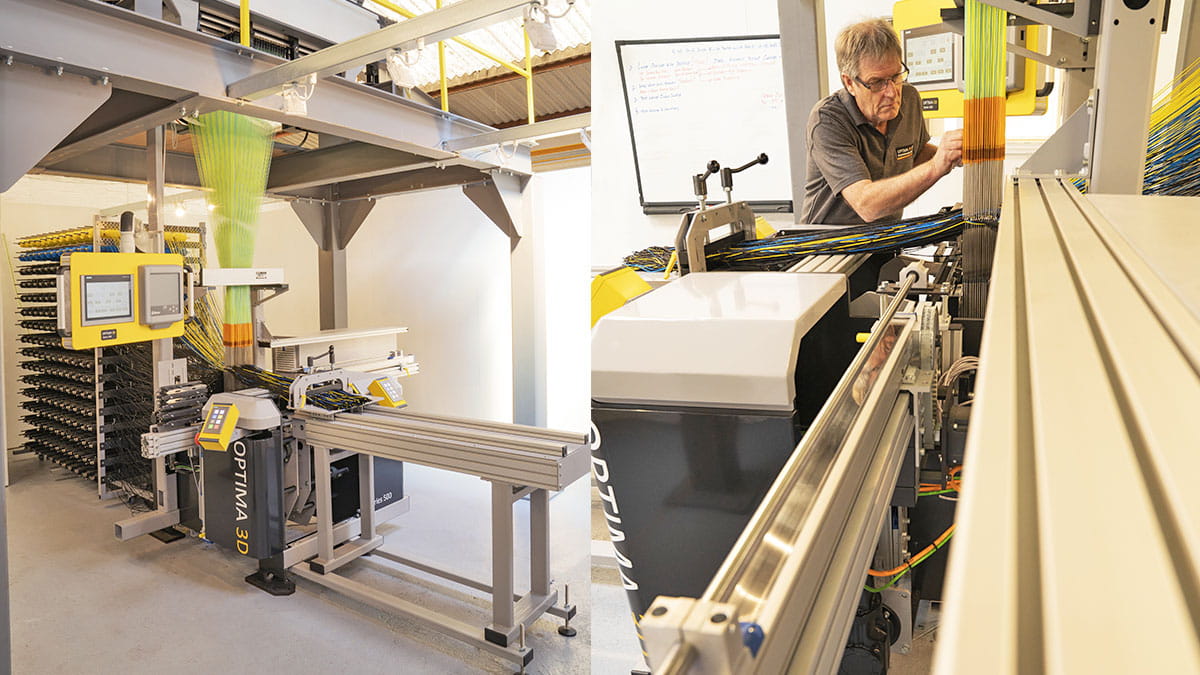
Optima 3D 500 Series offers a new point of view to 3d weaving
Optima 3D Chairman Peter Bryant stated that their vision to design and manufacture the new 500 Series offers a fresh perspective on the technology of 3D weaving machines. Bryant said; “This vision is to produce a machine that delivers real benefits to our customers; a machine that is simply better by design. This has resulted in the Series 500, 3D weaving machine which can cost effectively deliver both high quality and consistency. We are passionate about using cutting edge technology to enhance our machine and produce the best results for customers”.
The advantages of 3D weaving
A primary benefit that can be obtained in the production of composites with 3D weaving; is increased structural integrity due to the reinforced woven shape. The utilisation of a loom to weave interlocked Warp and Weft yarns between layers and through the thickness of the fabric; with further continuous interlocking of Weft yarns via Shuttle. This results in a 3D composite material that is better able to cope with impacts; or loads such as bending, without delamination. Research has indicated that such processes can produce materials; that exhibit fracture toughness up to 20 times higher than conventional laminates.