Evonik, known for its innovative, profitable and sustainable solutions in the field of chemistry, offers ready-to-use formulations to the additive manufacturing market with the INFINAM® brand. The company’s years of expertise in polymer chemistry enables numerous 3D applications. Lately, Evonik has introduced a new carbon-fiber reinforced PEEK filament, for use in 3D-printed medical implants. This last innovative smart biomaterial can be processed in common extrusion-based 3D printing technologies such as fused filament fabrication (FFF).
By presenting a new carbon-fiber reinforced PEEK filament, Evonik boosts 3D-printable biomaterials for medical technology that can be used for manufacturing. 3D-printable biomaterials have a key role in terms of sustainability while it can be used for medical implants with permanent body contact based on VESTAKEEP® PEEK as well as medical implant devices with temporary body contact based on the RESOMER® line of bioresorbable filaments and powders.
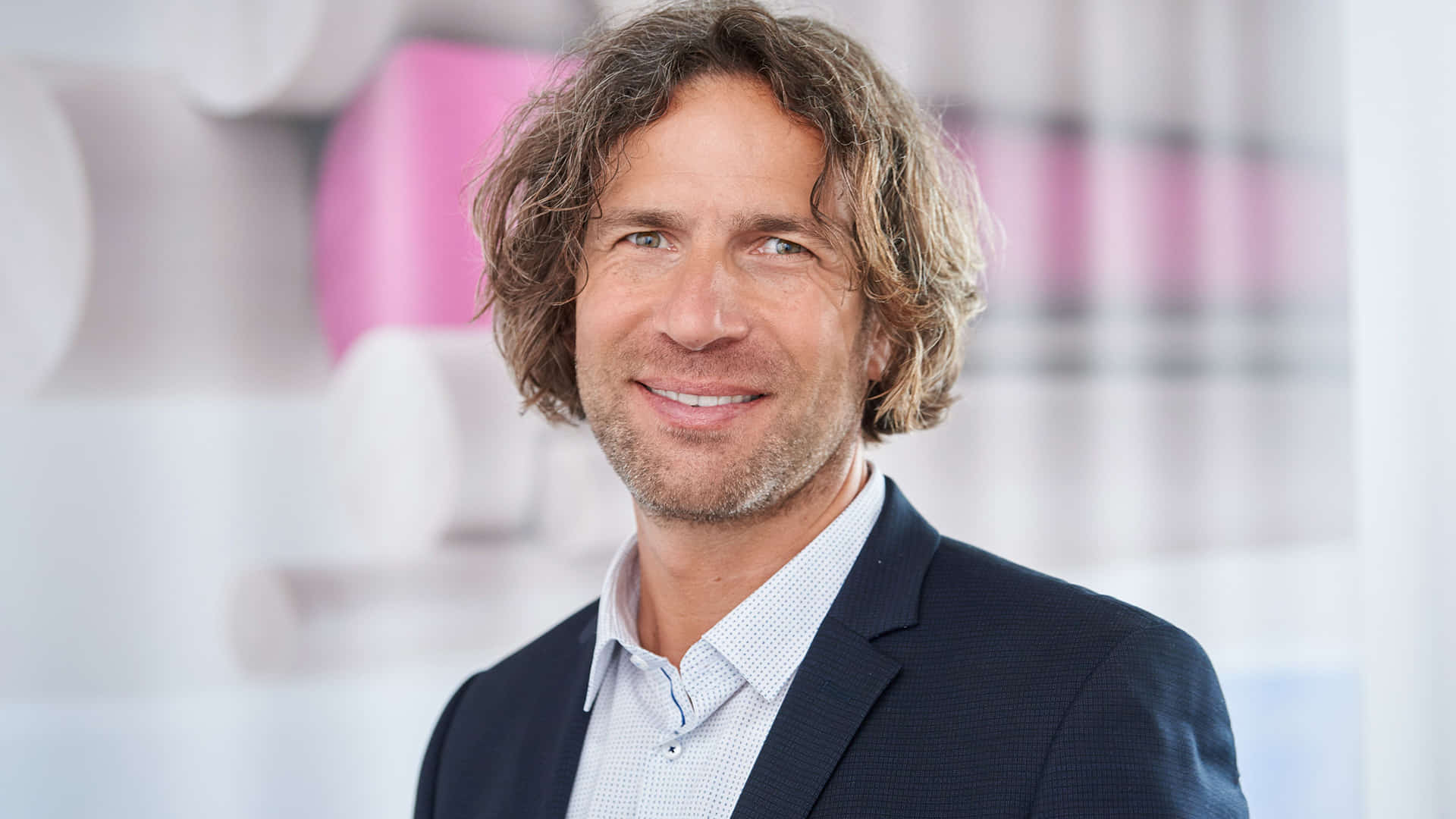
Evonik introduces the benefits of VESTAKEEP® iC4612 3DF and VESTAKEEP® iC4620 3DF
The two filaments, designated VESTAKEEP® iC4612 3DF and VESTAKEEP® iC4620 3DF, have carbon fiber contents of 12% and 20%, respectively. Depending on the strength and flex requirements for 3D printed implants like bone plates and other reconstructive prostheses, the two filaments provide a choice of material. Evonik’s VESTAKEEP® iC4612 3DF and VESTAKEEP® iC4620 3DF provides huge benefits with the ductility of its PEEK component. Furthermore, the product enables to specify the carbon fiber alignment throughout the 3D printing process by offering high biocompatibility for individuals with metal allergies without x-ray artifacts.
Head of Medical Systems at Evonik Marc Knebel remarked that by introducing carbon-fiber reinforced PEEK filament, they have opened up new possibilities in today’s medical technology for patient-specific treatment. Knebel emphasized the benefits of their technology as follows: “No other application field showcases more the advantages of 3D printing, such as individualization or design freedom, than medical technology. In trauma applications, for instance, 3D printed solutions offer an enormous time advantage over traditionally manufactured medical devices. It is conceivable that patient-specific solutions can be manufactured within two or three days, significantly improving the recovery phase.”
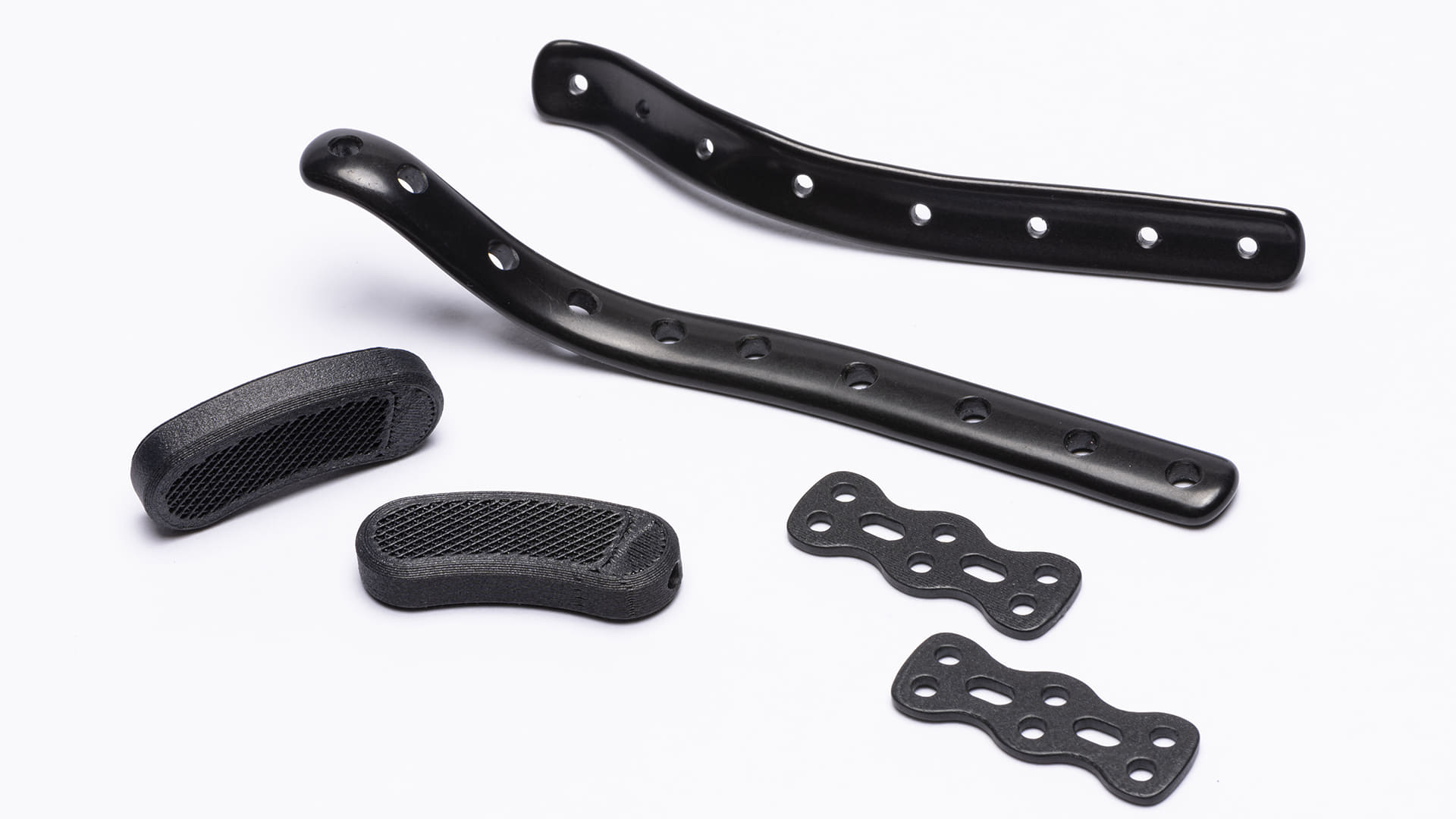
“We combine a unique set of competencies in materials science”
Evonik’s VESTAKEEP® iC4612 3DF and VESTAKEEP® iC4620 3DF have a 1.75 mm diameter and are available on 500g and 1,000g spools, respectively. These products can be utilized right away in FFF/FDM 3D printers for PEEK materials. The filament is put through rigorous quality control for medicinal goods. Indicating these advantages, Knebel stated that they will showcase the new product for the first time at coming next medical technology and 3D printing related trade shows and disclosed: “As passionate experts with decades of experience in polymer chemistry, we combine a unique set of competencies in materials science, manufacturing technologies and regulatory expertise to customers to accelerate time-to-market of new medical technologies for people’s lives beyond limits.”