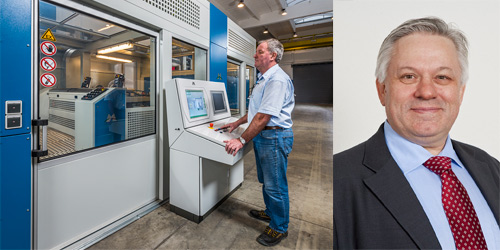
A. Monforts Textilmaschinen, the leading dyeing, finishing and compressive shrinking machine manufacturer, will be presenting its latest stenter for technical and filtration textiles at Filtech, a leading filtration exhibition that will take place from 11-13 October in Cologne, Germany.
The Montex 8500TT stenter is said to be ideal for the preparation of filter materials offering a stenter frame for drying and finishing of woven and nonwoven materials, high stretching devices in length and weft direction up to 10 000N and with high operating temperature up to 320°C.
Technical features
Optionally it offers coating and printing heads for the application of chemical compounds, together with Padders and Foam-Padders for foam and liquor applications. Belt dryers for light, as well as very heavy materials, are available. The stenter features chains with pins and clips or the combination of both.
Calenders for the flattening and compaction of the filter materials can be added offering working widths from 80cm up to 7m. Explosion proof versions and dryers are available for treatment with solvents.
Machines for filter materials
A. Monforts offer a wide range of production machines for filter materials that are being produced in Europe. According to Jürgen Hanel, Head of Technical Textiles, Monforts developed the first stenter with the possibility of thermosetting PTFE without oil greasing in the stenter chain and in the width adjustment. “This protects workers and the environment from harmful oil vapours and keeps the filter material clean,” he said.
“The guarantee of reaching 320°C with a very low temperature tolerance and with an excellent housing insulation is a major argument, so that we never reach an outside temperature over 60°C, at any position.”
Nonwoven applications
Further, the foam padder is designed to be able to run two different foams at each side of the material. For nonwoven applications this is recognised as a cost effective applicator whist retaining the porosity of the materials, the company reports. This applicator, after modification, can be used for thick felt and woven materials.
“With the foam solution our customer saves drying costs and can run much higher production speeds compared with a liquid padder,” explained Mr Hanel.