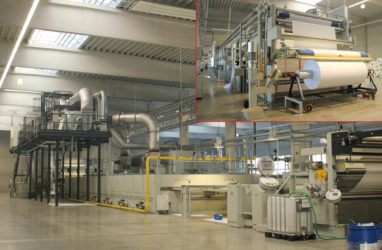
New German company GtA is running 24 hours a day to meet digital printing demand with purpose-ordered Monforts Montex 6500 stenter.
A new standard in pure white, 100% clean and fault-free textile substrates is being demanded by the rapid growth in digitally-printed banners and hoardings – often referred to as ‘soft signage’.
In response to this demand, a new company, GtA (Gesellschaft für textile Ausrüstung) has been formed and has erected a purpose-built plant on a greenfield site in Neresheim, Germany.
The plant has been equipped with a fully-automated 72 metre long installation comprising a washing machine integrated with a 3.6 metre wide Monforts Montex 6500 stenter.
The seven-chamber Montex stenter – purpose-built in Austrian Monforts production facility “MONTEX Ges. m.b.H.” – is equipped with a horizontal chain, a padder and an integrated weft straightener.
GtA is being run by a seasoned team of textile professionals led by Managing Director Andreas Niess, with the backing of Georg + Otto Friedrich – one of the largest manufacturers of warp knitted textiles in Europe.
With two production plants in Germany and headquartered at Gross-Zimmern, close to Frankfurt, Georg + Otto Friedrich has a monthly production of more than 450 t of warp knits – the equivalent of around six million metres – for a range of end-use applications, including garments, automotive interiors and technical textiles, in addition to digital printing substrates.
It is for digital printing, however, in addition to certain interior fabrics, which are washed and treated at the Neresheim plant, that GtA has been established.
“I have worked with other stenter manufacturers in the past, but we opted for Monforts technology and the company’s excellent service we have received’ says Andreas Niess.
Zeki Yagiz, Production and Quality Control Manager agrees. “We are fully in control of all production and quality parameters with this line,” he says.
The substrates of choice for digital printing are 100% polyester warp knits which have extremely smooth surfaces. This is becoming increasingly critical due to the general move away from PVC coatings; which were the standard in the past.
In addition, they are resilient and allow excellent take-up of inks; and vibrant colours and clear and precise images to be achieved with digital printing techniques. The knitted construction also has the advantage of elasticity, which is a plus in terms of flexibility for installers.
The raw fabrics to be finished are supplied by Georg + Otto Friedrich to GtA in weights of 50-350 gsm in rolls of up to 600 kg or 1800 metres. Depending on the fabric weight, GtA is running the stenter at speeds of between 20-50 metres an hour at an average temperature of 200ºC.
The entire finishing line is controlled by an EVA quality inspection and control system; which analyses every square metre of fabric; to ensure completely uniform and blemish-free production.
Another distinctive feature of the line is the proprietary addition to the Monforts air-to-air heat recovery system; which is now standard with Montex stenters. The GtA line is also configured for air-to-water heating to save considerable energy in washing operations.
The complete demand for hot water is generated by the heat exchanger; which also ensures surplus water for heating the building and the roof.
In addition, GtA has purpose-designed the automatic chemical mixing and dosing system; that feeds to the padder for the seven key treatments; that are carried out on the fabrics through the stenter.
“Here too, we have an extraordinary precise quality control and usability,” explains Andreas Niess. “Our daily philosophy is zero mistakes enforced throughout the company.”
Also fully automatic, are the roll inspection tables after the winder and a robotised cutting and packaging system; which converts the master rolls down to 75,100, 200 or 300 metre packages; to be dispatched back to Georg + Otto Friedrich and its many distributors; and partners ready to be printed.
The finished rolls are automatically glued with RFID labels and embedded in to the company’s own system.
GtA started production in February 2016 and for the first five months ran a single eight-hour shift. In July last year this was increased to two eight-hour shifts daily and since January this year; the company has been operating a three-shift system 24 hours a day; such is the need for its fabrics.
Around 14,000 metres of digitally-printed materials
One of the biggest projects the company has been involved with Georg + Otto Friedrich to date; was the supply of around 14,000 metres of digitally-printed materials; for the flags and banners of the Olympic Games in Rio Janeiro.