Zimmer Austria, a machine manufacturer for screen and digital printing, coating, drying and steaming, leads the development of a new special industry: digital military camouflage printing. The company with a lot of experience in its field, added digital military camouflage to its application areas about 3 years ago, besides strengthening its core markets; carpets, terry towels, upholstery, transportation fabric, technical textiles and narrow fabrics. Now, it has printers in operation in various countries and continues its R&D studies to meet the special demands of military camouflage. As Textilegence, we talked about Zimmer’s story in this special industry and the technical details with the CEO of Zimmer Austria, Digital Printing Systems Andreas Rass.
Rass explained that they had a request to run some camouflage prints for the first time about 3 years ago and noted that at that time they did not know too much about military camouflage and its complications. Saying that since then they have gained a lot of know-how and experience, he mentioned the strict specifications that camouflage printing has to follow in regard to colour, infrared reflectance and all kinds of fastness properties depending on the final application. Rass expressed the details as follows:
“Especially, infrared control makes military camouflage printing difficult because it requires in most cases very selected inks and software. It is a kind of 4th dimension besides the L*a*b (CIELAB) colour space values of the colour which can be seen. We also learned that almost every country has its own colours but also unique requirements in infrared reflectance in the range of 700 to 1400 nm.”
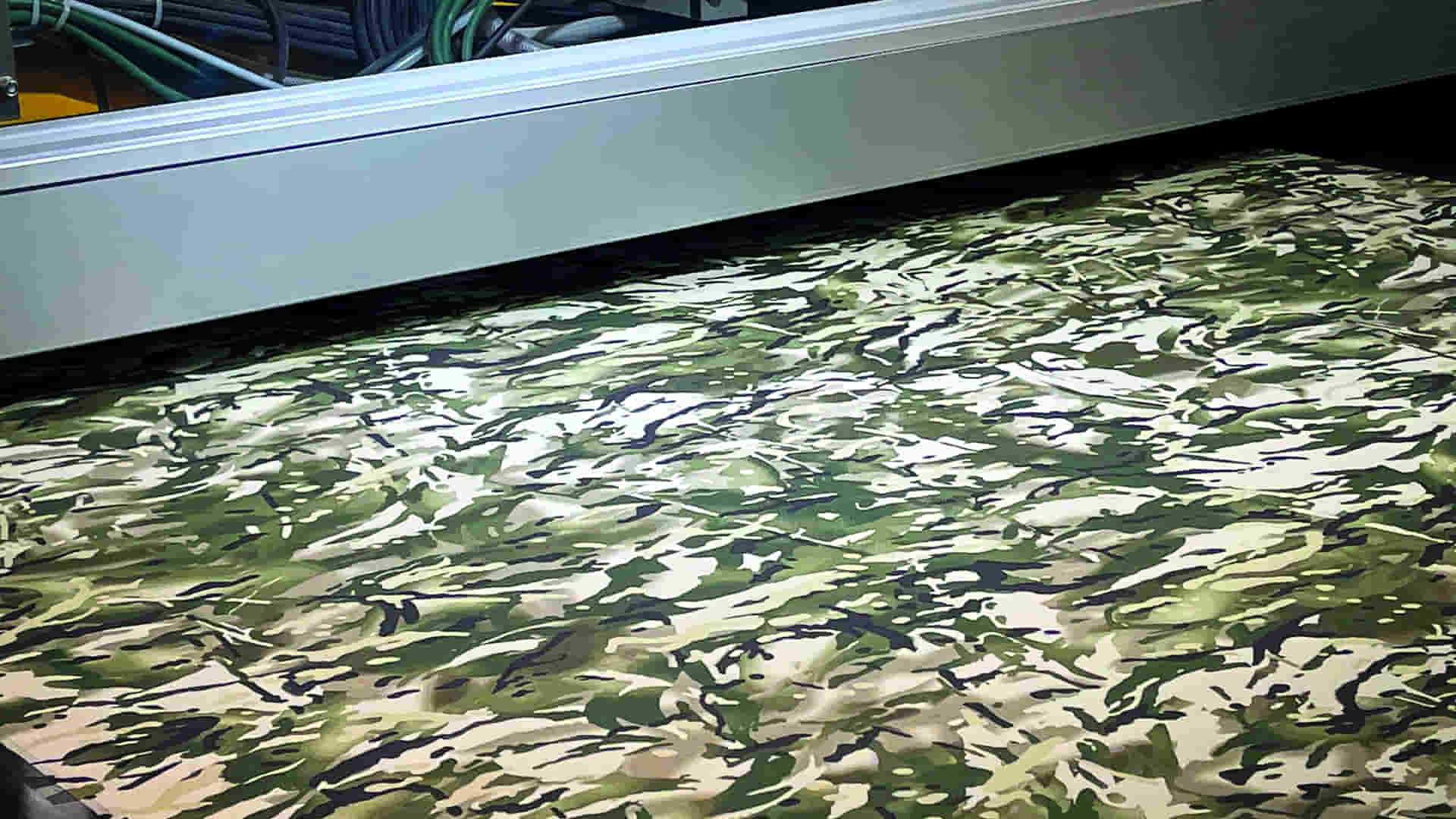
“Military camouflage printing requires special inks for different applications”
Zimmer Austria has solutions for most of the specifications: acid for polyamide; vat for polyamide/cotton; disperse for polyester; pigment for aramides and other mixed fibres but also for coated fabric. Andreas Rass disclosed that in this context, they work with some partners which develop special inks needed to match the specifications. Noting that each ink class has its own process, he continued his words as follows:
“In some cases, we also use two ink classes at the same time to reach the specification. Especially for camouflage, we offer a Colaris model with 8 or 16 colours in 2.2 m width with print speed up to 7 m/min. In military camouflage printing, we have to differentiate between regular army products which are still printed in high volumes using our rotary screen printing technology. But for special forces, camouflage covers and development work, digital printing has a clear advantage because of flexibility, unlimited number of colours and repeat size.”
Rass added that there are already a couple of printers in operation and said that some of them are for military webbings out of polyamide or polyester and some of them are for fabric out of nylon and/or mixed fibres using pigment ink.
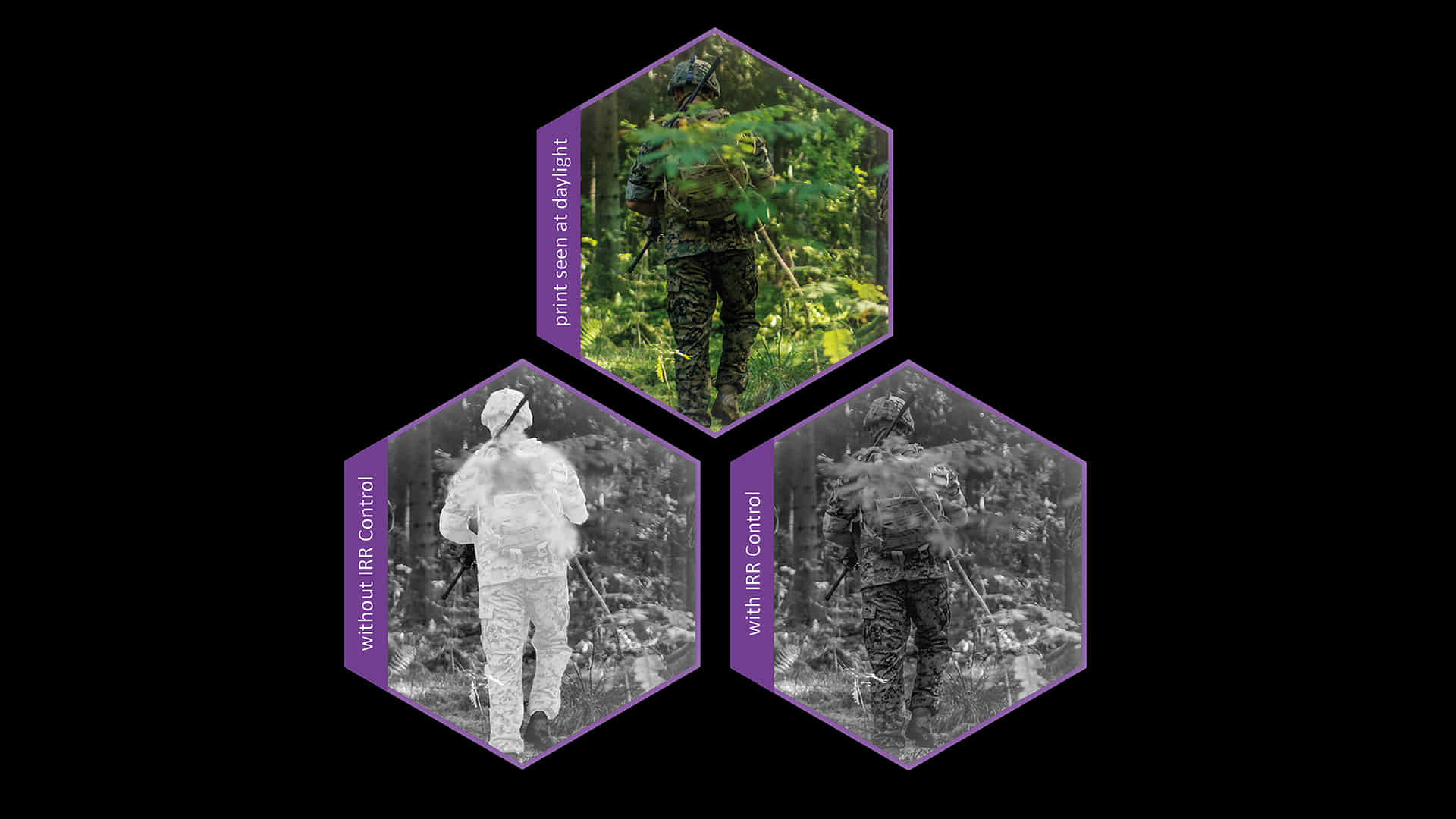
“We can open up the door for printers in military printing projects”
Mentioning his reviews on the future of the military camouflage printing market, Andreas Rass stated that they see a lot of interest in this special industry. Rass relayed that they expect a number of orders in the short and medium term, saying: “Digital printing in combination with our know-how could open up the door for printers which are not yet involved in military printing projects.”
Rass disclosed that they are still working on a number of special projects like prints on FR-coated nets and aramid products and explained that their other goal is to print on polyester/cotton fabric using disperse and vat dyes. He added that they also work on different software projects to simplify colour- and Infrared Reflectance matching.