As compressed air solutions, compressors are indispensable parts of an industrial production. Compressors produced in different types and features are designed in accordance with the unique demands of each sector. Established in 1968, Lupamat Compressor stands out as one of Turkey’s most powerful and efficient compressor brands. The company produces compressors of different types and capacities suitable for every sector, and also offers a significant added value to the Turkish economy, as it produces locally.
Lupamat Compressor Domestic and International Marketing Manager Tolga Kaynar made a statement to Textilegence about the work of the Izmir-based company and its solutions for the textile industry. Underlining that they have 50 years of experience in the compressed air industry, Kaynar explained the company’s development history as follows; “Lupamat Compressor, which has been manufacturing compressors for many years, joined the Dirinler Group in 2000 and entered a rapid development period. Group includes; Dirinler Makine Sanayi (eccentric and hydraulic press manufacturing) established in 1952, Dirinler Sanayi Makinaları (CNC, lathe, vertical machining bench, double column machining/milling) and Dirinler Döküm Sanayi (wind energy industry, shipbuilding, manufacture of valves and pumps with large and heavy parts for the building industry and heavy industry). Lupamat Compressor continues to be the pioneer of innovations in the sector by using the advantages provided by these group companies, which are industrial powers on their own”.
Disclosing that Lupamat exports to more than 50 countries, Kaynar said that they have a wide range of products and they have special solutions for each sector. Kaynar said; “Reciprocating compressors for small businesses, high efficiency screw and reciprocating compressors for medium and large enterprises, oil-free compressors preferred by the food, health and electronics sectors are among our solutions”.
Reminding that they opened an R&D centre in 2018, Kaynar stated that the high value added products developed here have gained importance in the portfolio. Kaynar emphasized that the new generation compressors; developed and manufactured with Industry 4.0 compatibility in mind; are energy efficient, highly productive; and have smart features such as 24-hour monitoring, control and feedback.
Lupamat Compressor offers textile-specific solutions
Textile is one of the main sectors where Lupamat Compressor provides solution. Tolga Kaynar said that with their rich product portfolio; they have become a preferred brand for all applications in the textile production process. “Our compressors respond clearly to the needs of textile manufacturers, both with their hardware and their longevity. They make a difference in the industry with these features,” said Kaynar; and stated that the new generation low pressure high efficiency compressors developed especially for texturing got full marks from the customers.
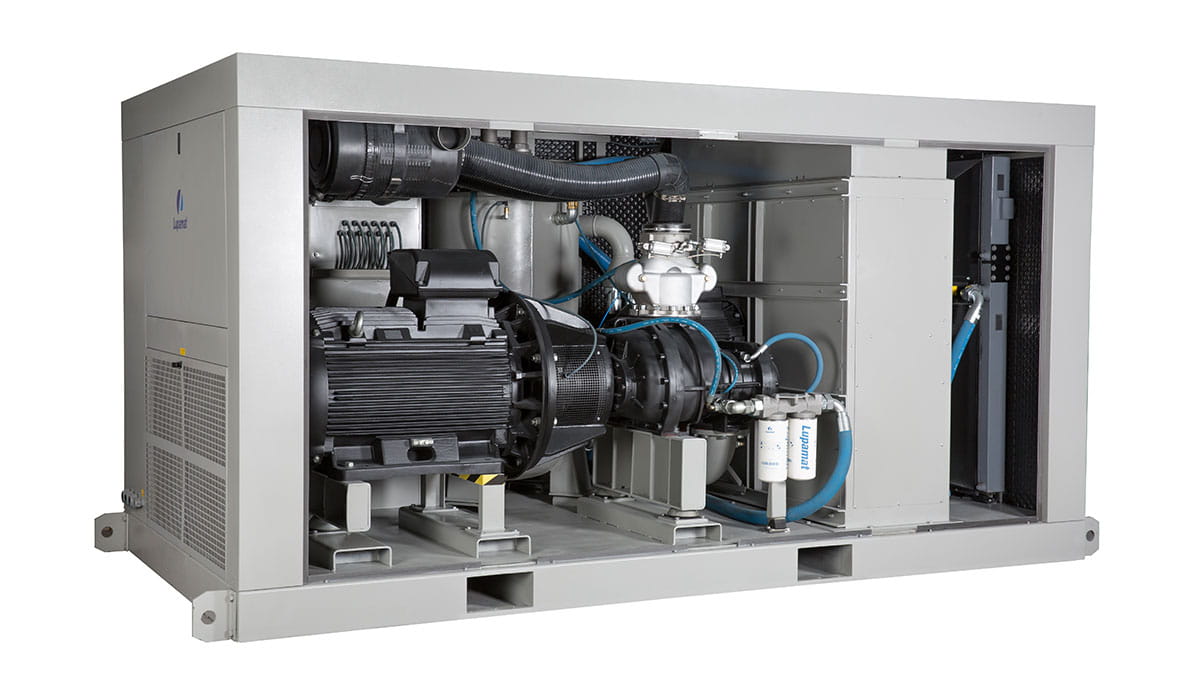
Expressing that synthetic yarns are likened to yarns produced from natural fibres and gained superior properties in the texturing process, Kaynar continued as follows; “It is very important for textile manufacturers that our compressors show maximum efficiency especially at low pressure. These compressors; which we have developed in line with the needs and demands of the textile industry; show maximum performance no matter how bad the ambient conditions are”.
Explaining that they are in direct contact with the customer during the compressor purchase and installation process; Kaynar stated that the customer demand is handled in detail. Kaynar summarized the progress that follows; “We make detailed analyses from which compressor model will be suitable; where to place it, from air installations to points of use, analysis of current air demand and power consumption. In this way, we reduce our customers’ compressed air production costs. We create a sustainable and efficient compressed air systems for them. Since each facility is different from each other, we do this process separately for each company. As a result, we offer a customized solution to the customer”.
Exports increase with value added products
Tolga Kaynar stated that they managed to produce high value-added compressors that appeal to different sectors with their R&D studies. Kaynar noted that they have recently introduced the carbon dioxide (CO2) compressor preferred by the food industry to the market. Kaynar said that the bacteria is prevented from entering the package with the CO2 compressor ensuring that the product will last for a long time; and continued his words as follows;
“This product is in high demand from the food industry, especially for alcohol, soda and carbonated drinks. Thus, the shelf life of the products is extended and the product reaches the end user without spoiling. Being the first and only manufacturer of this compressor in Turkey; Lupamat Compressor is increasing its strength in the domestic and overseas markets with value-added products. We made the first sale of this product to India”.
Indicating that the rail system compressors produced in 2017 proved the success; Kaynar stated that these products were used extensively in opening and closing the doors of the wagons, pantograph devices, wipers, and braking systems. “We are the first manufacturer of oil-free rail system compressors in Turkey,” said Kaynar; and mentioned that this product is developed with their Japanese business partners.
Stating that the R&D department is working on new areas of application, Tolga Kaynar shared the information about the work on electric bus compressors. Kaynar; “These compressors are small, compact, oil-free compressors that allow doors to open and close. We aim to bring it to the market by the end of 2020”.