Drawing on a database of more than 40,000 apparel design patterns and a highly-integrated production structure, İlay Textile, based in Bursa, Turkey, is one of the leading players in the Turkish textile industry. Working with the vision of innovative production in textile and apparel, the company responded to the sustainability and energy efficiency demands with Monforts in its new finishing investment. The company is a specialist in the provision of rapid and creative solutions to meet the continuously changing needs of the fashion world, and has strengthened its hand with the Monforts Montex stenter installation.
Founded in 1992 and started exporting the next year, the company gained a reputation among the leading Turkish brands as well as its customers in Europe with its leadership in new printing techniques and technologies. Having a dedicated workforce of more than 500 people, İlay Tekstil has weaving, warp knitting, dyeing, finishing and printing operations as well as final garment making-up and packaging departments in its factory of over 50 thousand square meters.
İlay Tekstil Production Director Fikri Savaş emphasized their export-oriented power by saying; “We supply to customers in Germany, France, Italy, the Netherlands, Spain and the UK; including to major brands such as Inditex and Otto”. Savaş continued his words as follows; “We opened offices in Barcelona in 2015 and New York in 2017; in order to both consolidate and expand our geographical reach. Sustainable production is very important to both us and our customers. We want to improve on this with every new technology investment we make”.
The mission is error-free and resource-efficient production
Working with the mission of continuous progress in error-free and resource-efficient production; İlay Tekstil has therefore invested in Monforts Montex stenter. The Montex stenter range has a working width of two meters and eight TwinAir chambers; and contributes to the company’s mission.
Relaying that this installation provides them with much improved control options for all process parameters; Fikri Savaş noted that compared to the old stenter it is replacing, they are particularly impressed with the energy savings they are making.
Key focus on Montex stenters is energy savings
Achieving energy savings on Montex stenters has been a key focus for Monforts designers and engineers in Germany for many years.
With the TwinAir heating chamber system within a Montex stenter; top and bottom airflows can be regulated completely independently of each other; ensuring heat is only applied when and where it is required. The Optiscan balancing system ensures continuous automatic evaluation of the distance between the nozzles and the fabric for highly economical and contact-free drying.
The resulting constant evaporation rate within the stenter ensures optimum energy utilisation. In addition, TwinAir chambers feature special panelling for low heat radiation; careful sealing of all connecting positions and chamber access points, and air locks at both the entry and the exit.
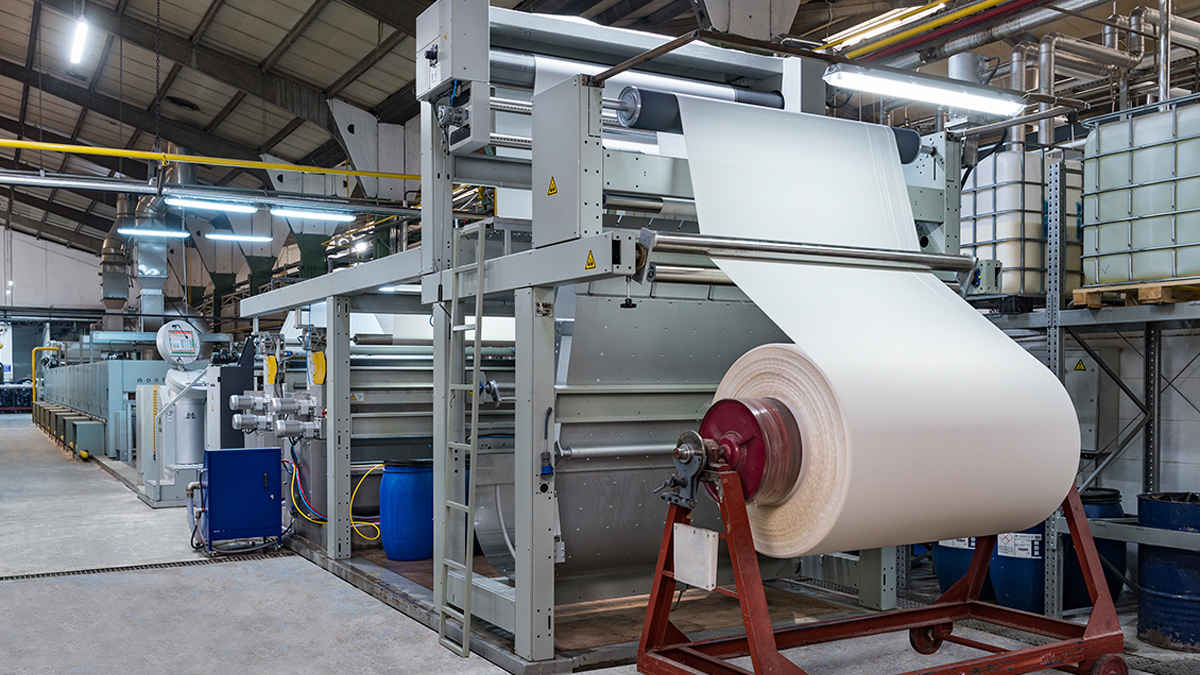
Monforts stenters set the benchmark in terms of energy efficiency
Ahmet Kılıç, founder of Neotek, the representative for Monforts in Turkey commented; “Monforts stenters set the benchmark in terms of energy efficiency and help conserve resources”. Kılıç continued his words saying; “Automatically setting the initial moisture content requirement for a specific process before drying to a minimum value; helps reduce heat evaporation and consequently, energy consumption. The hermetic sealing of the stenter frame further prevents the loss of heated air; as well as the ingress of excessive cold air – which has to be heated back up if it is not kept out in the first place”.
The new Montex line was completed at İlay Textile in August 2020, with no problems during either installation or commissioning. Fikri Savaş stated that the owners of Neotek carefully followed the assembly process and concluded his words saying; “They supported us in every way so that we could produce with the machine as soon as possible. The technicians who installed the machine and put it into operation were very sociable; and worked very harmoniously with our own team”.