Groz-Beckert, one of the leading suppliers of industrial machine needles, precision parts and precision tools, as well as systems and services for textile surfaces, increases the sector standards with its collaborations. The company developed the optimized Relanit sinker SNK F together with the German circular knitting machine manufacturer Mayer & Cie. in the past years, independently of this, also developing the new LCmax™ energy-saving needles. The focus of both developments is on efficiency, energy savings and increased process reliability. At the ITMA in Milan in June 2023, Groz-Beckert presented some of the successful cooperation under the motto “Innovation through cooperation”. Among them, these two new developments realized with Mayer & Cie. Groz-Beckert were presented.
Optimized Relanit sinker SNK F
At the end of 2018, circular knitting machine manufacturer Mayer & Cie. approached Groz-Beckert with a request to jointly develop an improved and more efficient sinker for selected machines of their Relanit family that would run more smoothly and reliably in the needle tricks. Featuring an integral spring with a spring force adapted to the sinker thickness, the new sinker has proven its functionality and advantages through successful field tests.
Thanks to their unique, adapted spring, the newly developed SNK F Relanit sinkers are securely guided while they are running through the cam track, resulting in a quieter operation. This increases process reliability and ensures an improved loop structure. In addition, wear on the swivel butts of the sinkers is reduced. This increases service life and makes the process more sustainable and cost-efficient.
Higher energy efficiency thanks to LCmax™
The second recent cooperation with Mayer & Cie. was initiated by Groz-Beckert. The objective of this project was to develop a cost-effective and energy-saving needle. After evaluating various options, the joint choice of Mayer & Cie. and Groz-Beckert was the LCmax™ knitting machine needle with its innovative, wave-shaped shank geometry. The first prototypes were extensively tested on laboratory machines at Groz-Beckert’s Technology and Development Center (TEZ). Trials proved the advantages of the new technology.
The innovative, wave-shaped shank of the LCmax™ needle ensures a smaller contact area of the needle in the needle trick. This results in less friction, which reduces machine temperature and enables energy savings of up to 20 percent compared to a standard needle. This saves costs and at the same time allows the operation of the machine at the maximum possible speed.
In both projects, the cooperation between Mayer & Cie. and Groz-Beckert went far beyond mere product development. In addition to Applications Engineering and Construction, the companies’ Sales and Purchasing departments were also involved in a close exchange. The cooperation at all levels was characterized by openness, constructiveness, partnership and goal orientation, and led to successful results from which the customers of both companies can now benefit.
Groz-Beckert offers interested machine builders different cooperation options to jointly develop new products or optimize existing ones. The Groz-Beckert Technology and Development Center provides the appropriate framework for so-called co-development projects.
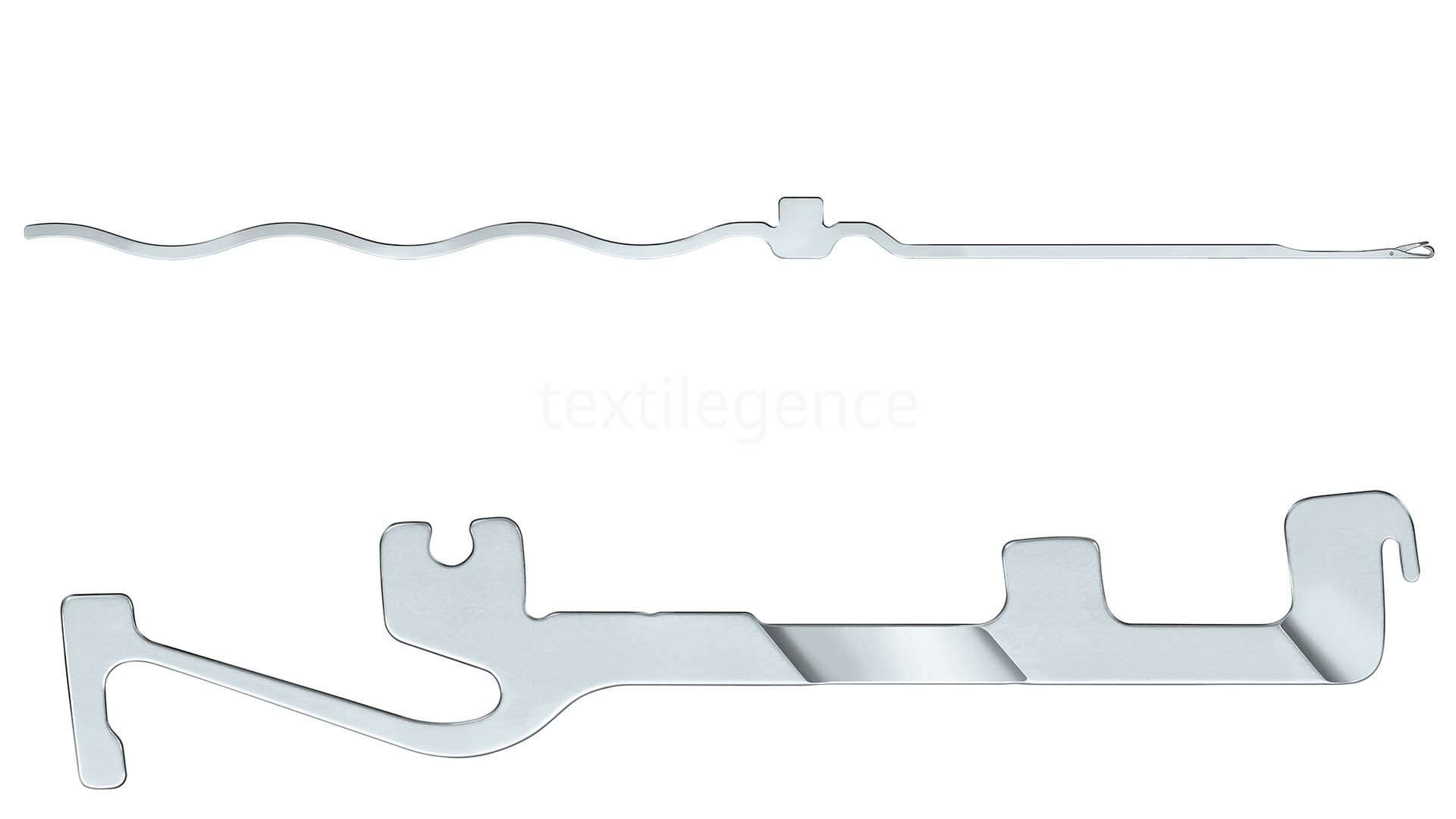
“We were very pleased with the performance of the new version sinkers”
Toraman Tekstil San. Ve Tic. A.Ş. made the following statement about the newly developed SNK F sinkers for Mayer & Cie. Relanit model machines: “We did not encounter any problems while installing the new sinkers into the channels. We used new SNK-F-OL 55.44-18 G 1 Relanit spring sinkers together with Groz-Beckert’s LS+ 90.41 G 0059 needles without any problems. During the usage period of this new sinker type, we produced 312.000 kg of fabric with OE Viscon, Vortex Viscon, Ring Viscon, OE Cotton, Ring Cotton yarns. We were very pleased with the performance of the new version sinkers.”
Buyruk Tekstil Konfeksiyon Ltd.Şti Knitting Department Manager Soner Boy disclosed: “In our Mayer & Cie. Relanit 3.2 HS 2018 model machine, as the new generation spring-loaded Groz-Beckert SNK F OL 55.44-18 G1 sinker and LS+ 140.41 G0086/87/88/89 series needle sets are used. SNK F OL 55.44-18 G1 Relanit spring sinkers operate smoothly in our machine at a speed of 45 RPM. In the usage phase of this sinker type 36/1 combed cotton, 30/1 combed cotton, lycra lacoste, lycra 2 thread, lycra single jersey and standard single jersey fabrics were knitted without any problems. The sinkers are still working in the machine and 200 tons of fabric have been produced since the day they were installed on the machine, and the estimated usage is 500 tons of production is targeted with this sinker type.”
Indicating that as a company they have decided Groz-Beckert SNK F OL 55.44-18 G1 spring type sinkers to be used in all their Relanit machines, Boy said: “We would like to thank Groz-Beckert for their support in minimizing the costs of knitting companies by producing such improved products and we would like to state that we are always ready to provide all kinds of support in such product development efforts.”
“One of the biggest advantages of LCmax™ needles is reducing costs”
Has Örme Tekstil San. ve Tic.Ltd.Şti. Business Manager Adem Aşıkuzun, expressed his opinions about the LCmax™ needles newly developed by Groz-Beckert for Mayer & Cie. Relanit model machines as follows: “New type LCmax™ 90.41 G 0060 needles are used in the 2016 model, 28 gauge Mayer & Cie. Relanit 3.2 II machine. The needles run at a speed of 26 rpm. Approximately 52.300 kg of 36/1 compact combed cotton (lycra) and 40/1 melange (lycra) single jersey fabric has been produced with these needles so far. The needles are still running and our target is to produce up to approximately 150 tons of fabric. We think that both short and long versions of this needle can be used in the other 28 gauge Mayer & Cie. Relanit machines in our company. One of the biggest advantages of this new needle type, which emerged as a result of Groz-Beckert’s R&D activities, is that it extends the maintenance time of the machine and reduces our production costs. In addition, less needle distortion was observed in this needle type during machine maintenance compared to the old type needle.”