We all know that necessity is the mother of invention, which is why, due to the lack of availability, mouth and nose masks were home-sewn – and the so-called community mask became a true design object. But what is in commercial face masks and how do they work? Groz-Beckert will provide the answers to these questions in this article.
The ‘simple mouth mask’ – also known as surgical mask – is designed mainly to protect the surroundings of the wearer; from germs that the wearer may spread by breathing or sneezing, for example. These masks usually consist of a triple-layer sandwich design (SMS) made from nonwovens:
Layer 1: Spunbonded fleece
Layer 2: Meltblown nonwoven
Layer 3: Spunbonded fleece
These three layers are usually joined with polypropylene (PP), which is thermally bonded. The meltblown layer made from PP microfibers is responsible for providing the germ and liquid barrier properties in these masks. The fine endless fibers in the meltblown nonwovens are up to 70 times finer than human hair and therefore have a fiber diameter with a thickness of just one micrometer in places. In contrast, a cotton fiber – which is often used to make community masks – is often between 12 and 35 µm thick, with a length of 15 to 56 mm.
The separation of particles, i.e. the separation of particles from the air flow, on filter-active layers works according to the following principles:
Sieve effect
Particles with a diameter larger than the pore diameter of the nonwovens are caught in the structure. This effect is irrelevant for these masks.
Inertial effect
Larger particles can no longer follow the air flow around the fiber, maintain their direction and meet the surface of the fiber which they are caught by.
Diffusion effect
Extremely small particles move freely and chaotically on their trajectory in the air flow. The additional level of movement increases the probability that they will come into contact with the fibers and be caught there.
Electrostatic attraction
The electrostatic charge of the fibers means that particles are drawn in by the fibers like a magnet and are held there (separated).
Although the spaces between the melt-blown microfibers are significantly smaller than those between cotton fibers, they can still be up to one hundred times larger than the Covid-19 virus (approx. 0.12 micrometers). A mouth and nose mask is therefore usually not sufficient to separate virus-bearing aerosols.
So-called FFP masks are used to separate droplets of liquid with the Covid-19 virus (in accordance with DIN EN 149). These filtrating half masks are respirators to provide protection against particles. They have a more elaborate design than the surgical masks, as multi-layer filter layers are used here in some cases and the mask follows the shape of the face. The quality class of the mask is determined by its ability to separate particles (in addition to other properties). The masks are divided into classes based on the degree of separation achieved.
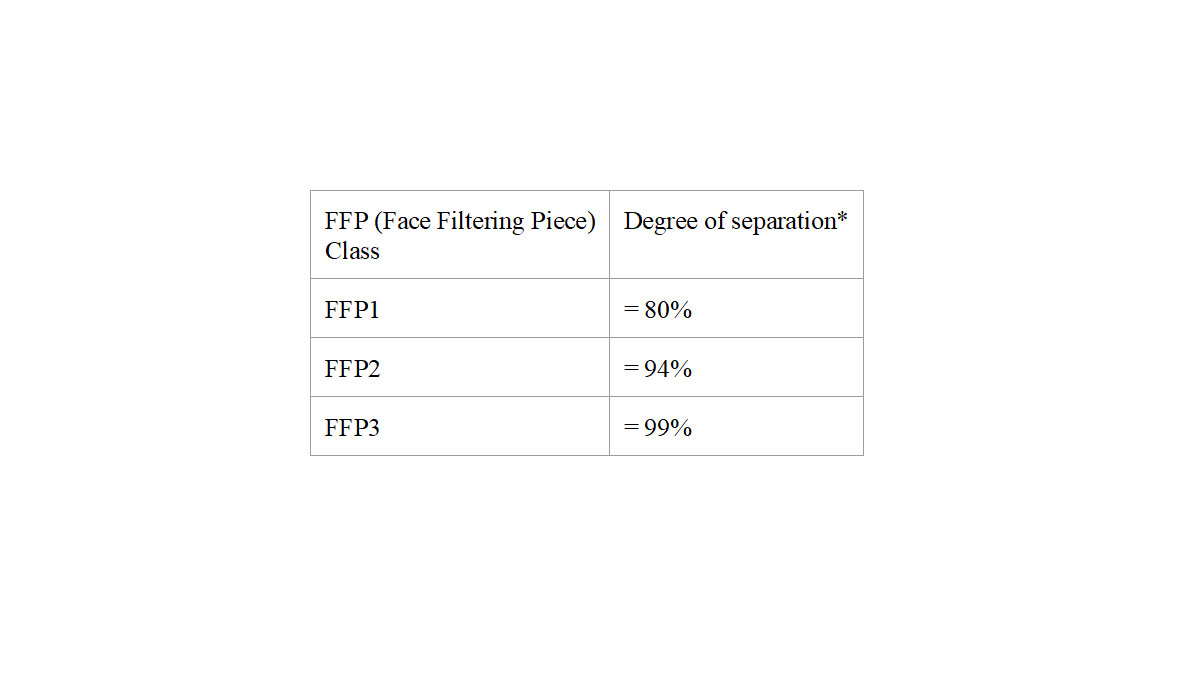
*95l/min for sodium chloride & paraffin oil test
The filtrating half masks can also be fitted with an exhalation valve. FFP2 and FFP3 masks with a valve protect the wearer from the smallest particles and aerosols from the air. Masks without a valve also protect the surroundings from contamination. Both classifications are recommended for protecting against coronavirus.
Depending on the country or region, different classifications, standards and quality classes are used to categorize the masks. In Europe, the EN 14683 standard applies, in China, the YY 0469 or KN standard is used (e.g.: KN95) and the USA use the N standard (e.g.: N95):
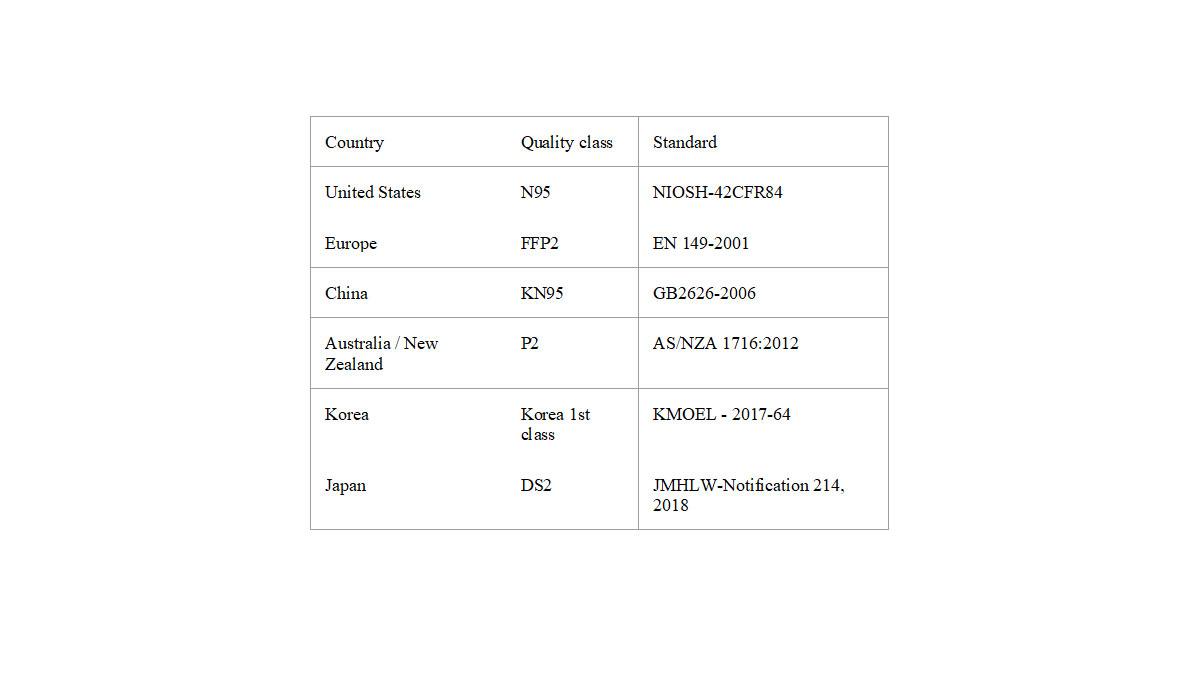
In addition to masks, other hygiene-related items are more in demand than ever. Body care and hygiene products, such as antimicrobial wet wipes or dressings and surgical materials are often manufactured via hydroentanglement. Jet strips from Groz-Beckert are used in this process, among other things.
But cleaning cloths for cleaning floors, disinfecting or general surface cleaning have also become more popular. Some of these are made using felting needles from Groz-Beckert.
Did you know?
In 2019, China became the largest exporter of medical protective equipment with a 17 percent market share. Germany was in second place with 13 percent, followed by the USA with 10 percent market share. The total value of protective equipment exported in 2019 was around 135 billion USD, which is likely to be exceed by 2020.