BB Engineering founded in 1998 as a joint venture of two leading brands in the machine building sector, Oerlikon and Brückner, has been in the market as a reliable partner in the field of machinery and plant engineering for the synthetic fiber and film industry since then. The company considers product development as adding value, continue to support its customers holistically. Dr. Klaus Schäfer, Managing Director of BB Engineering talked about the advantages of their solutions and answered our questions about 2024 reviews and forecasts for 2025.
Schäfer evaluated 2024 as a successful year, saying they worked on their customer projects and R&D activities as planned and concluded the year successfully. “We already have a good order intake for this year and are therefore looking positively towards 2025. With the orders we have already received, we are looking forward to exciting customer projects in the areas of recycling and air-texturing and expect further growth for our company,” he relayed.
He emphasised that sustainability is always a major issue for them and it means more than just the circular economy and reminded that things like energy saving and process efficiency are also of economic interest to every company. “These are and have always been important goals in our product developments, because we want to offer our customers added value. That’s why we call ourselves the “Valueneering Company”. We will maintain our R&D studies also on this perspective this year,” he expressed.
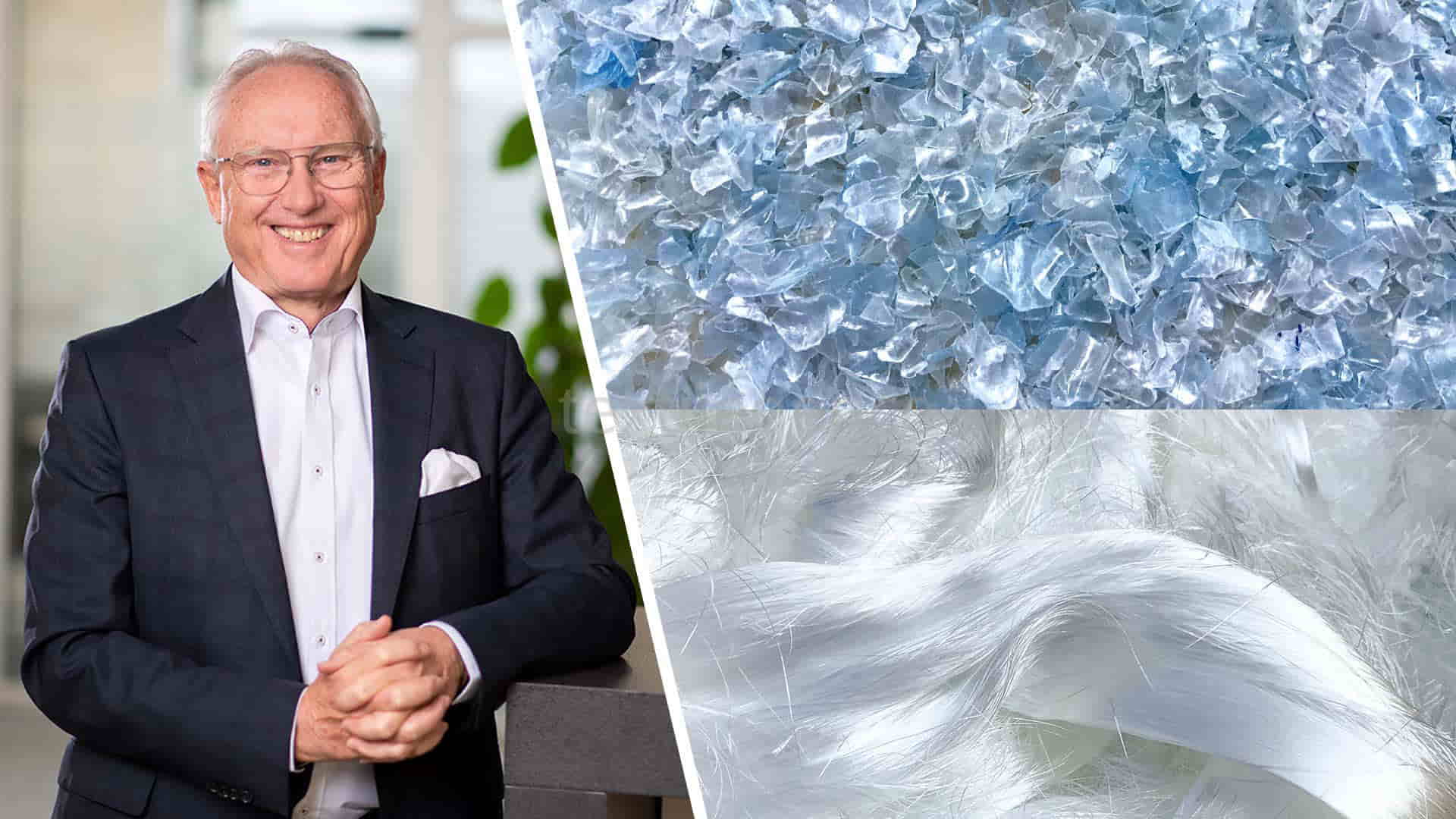
Schäfer said that for more than 25 years, they have been working and growing according to a special business model; “On the one hand, we are a know-how carrier and developer in the field of extrusion and filtration for our parent companies, Oerlikon and Brückner, and supply both of them with the corresponding hardware. At the same time, we make use of these technologies and have developed them into independent product lines for the global synthetic fiber market. We are very successful in the area of smaller, flexible spinning systems (VarioFil), air-texturizing machines (JeTex) and PET recycling systems (VacuFil). Our development activities in the field of recycling are also welcomed by our parent companies, as PET is also one of their core materials. Against this background, we also see good growth for our company in the future.”
“We are able to have better spinning properties with recycled material than virgin ones”
Dr. Klaus Schäfer shared the developments on the Vacufil recycling system launched on the market in the scope of sustainability in 2019, so far, saying that they registered a great deal of interest in the VacuFil recycling system. “We have since installed a test system in our technical center to carry out individual customer trials. This has been well received and we are achieving convincing results in terms of product quality and spinning properties of the recycled material,” he explained.
He underlined that BB Engineering had already been on the market with recycling before 2019; “With our VarioFil R, we offer a flake-to-fiber process. With VacuFil, we also offer our customers fiber-to-fiber, so that they can theoretically recycle and re-spin their own production waste including knitted fabrics directly. With our experience in extrusion and filtration behind us, we have developed a reliable process that is customized for each customer project. And we can proudly say that the recyclates from our technical center sometimes have better spinning properties than virgin material in our tests,” he relayed.
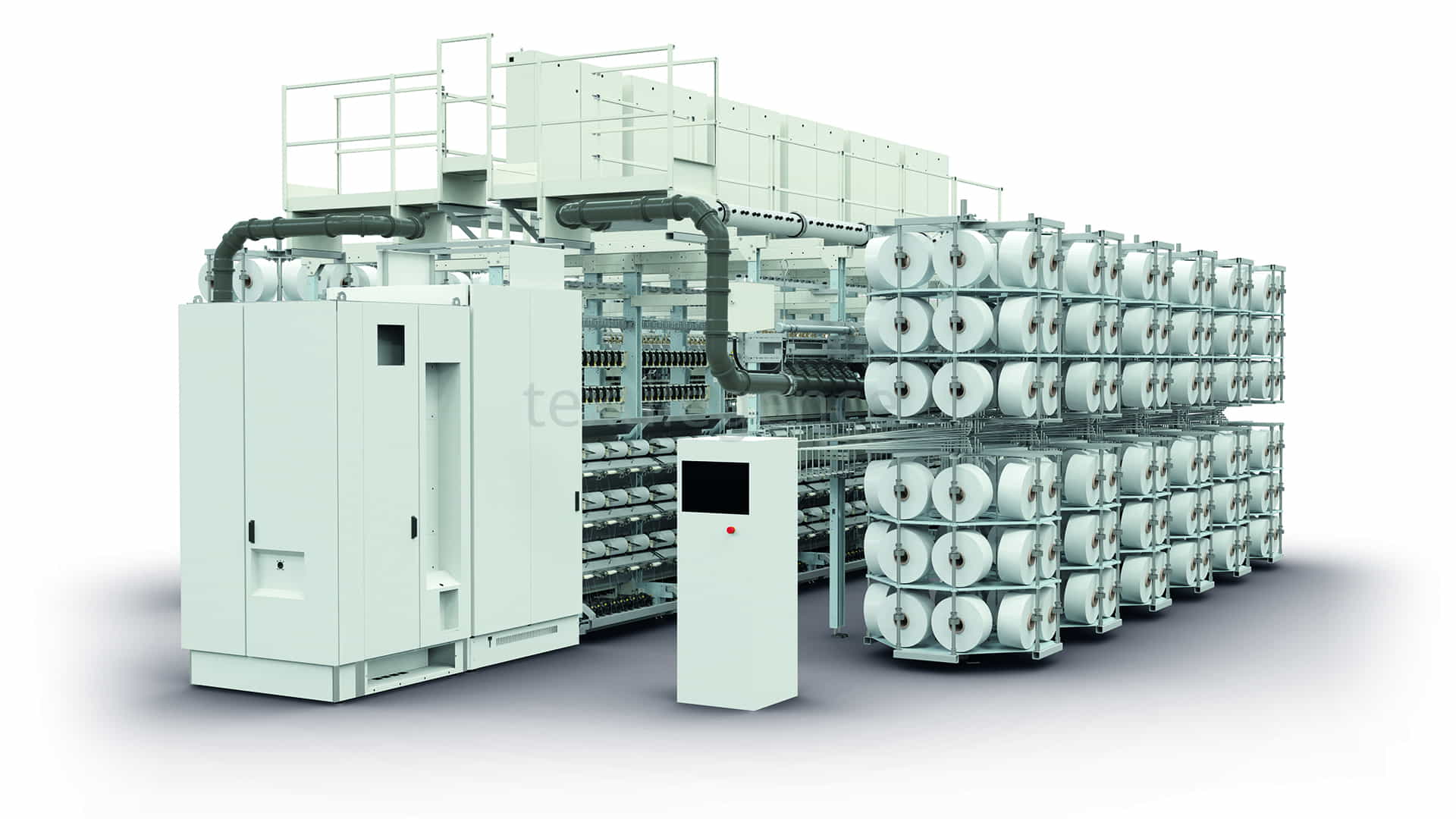
Stating that the biggest challenge in PET recycling of fiber and textile waste is the quality and uniformity of the source material, he continued: “For a stable and reliable process and thus consistent quality in the subsequent recyclate, the source material must meet certain requirements. This is particularly difficult with post-consumer waste, as the origin, composition, etc. are often not uniform. So, due to the lack of post-consumer feedstock, our customers focus on post-production recycling. Here, the origin is usually clear and, ideally, the in-house production and composition are fairly uniform. Deviations in viscosity are monitored by our viscometer and are regulated with our Visco+ LSP technology to achieve purest homogeneity.”
JeTex air-texturizing line offers producers flexibility
Mentioning a production line for high-quality air-textured yarn (ATY) JeTex, one of their innovations launched in recent years, Dr. Klaus Schäfer expressed that the system incorporates BB Engineering’s advanced texturizing technology, complemented by cutting-edge components from Oerlikon Barmag, ensuring high production speeds, consistent quality, and the desired aesthetic effects. He said that JeTex guarantees efficient, cost-effective production of high-quality air-texturized yarn by combining rapid output with low energy consumption and explained its advantages for the producers as follows: “In addition to our specially developed high-end texturizing box, a special feature of JeTex is that we not only offer it as a complete system, but can also convert existing state-of-the-art stretch-texturizing systems from Barmag to air-texturing, so that this innovative technology is also available for air-texturizing and producers can easily convert their machines.”
He expressed that this highly flexible system is available in various sizes and production capacities, with two independently operating subsystems. “It processes POY and FDY made from materials such as PET, PA6, PA6.6, and PP. The feedstock titer range spans from 30 to 600 den per single yarn end (for both core and effect filaments), while the final titer ranges between 60 and 1600 den,” he stated.
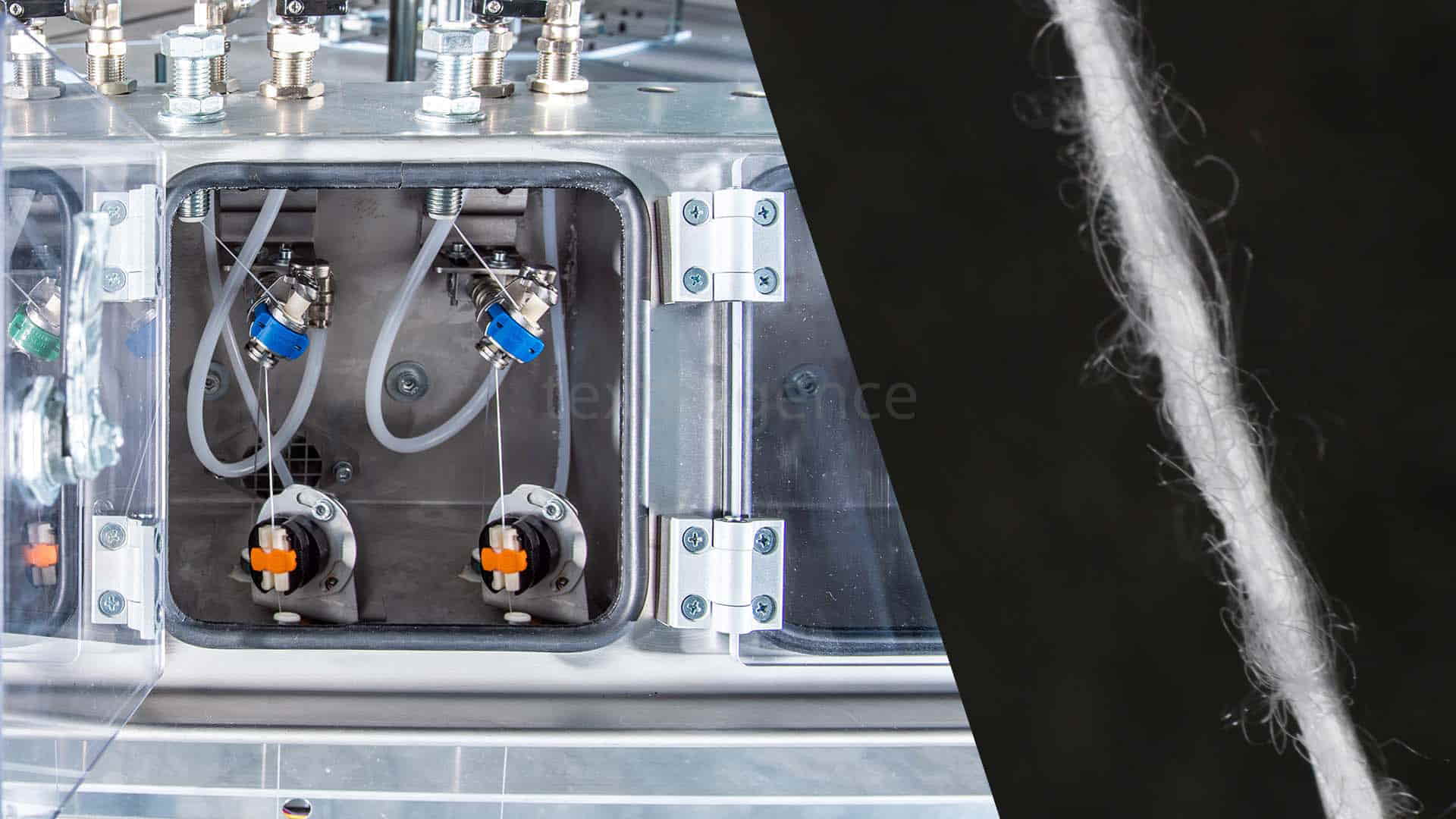
“We see a lot of potential in the Turkish market”
Dr. Klaus Schäfer, sharing his reviews on the Turkish market, emphasised that Türkiye is by far their most important market and they maintain long-standing business relationships. He stated that their representative Tekstil Servis is an important partner here: “Close and regular customer contact is very important to us. That is why we are always personally represented to our customers at the ITM at the Tekstil Servis booth and last year we successfully held a roadshow in Gaziantep and Bursa, where we presented our latest developments together with Oerlikon Barmag. We definitely want to repeat this. We are also optimistic about the future of Türkiye and still see a lot of potential in the market. This is reflected in the current customer interest. We are in project negotiations and are currently also implementing projects in Türkiye,” he said.