A single-apron drafting system can improve the uniformity of the spun yarn and the strength of the drawn sliver due to improved fibre control. The study ‘Advantages of Single-Apron High-Draft Systems’ was written by Research Associate Seyit Halaç from Institut für Textiltechnik of RWTH Aachen University with the contribution of Prof. Dr. Thomas Gries, shows that this solution also improves maintenance costs and energy savings since it uses a static fibre control element instead of one of the two aprons.
“In the air spinning process, high draft drafting systems are installed in front of the nozzle to draw and refine the sliver to the required yarn count. To achieve a controlled fibre guiding, the fibres are guided in the main drafting zone by double aprons, which have both technological and production-economical disadvantages,” says Research Associate Seyit Halaç, pointing out that novel fibre guiding elements can improve the efficiency of high drafting systems.
He reminds that the air spinning process was first presented in 1997 by Murata Machinery Ltd, Kyoto, Japan in the Murata Vortex Spinner and expresses that yarn production occurred in a single process stage without a flyer and winding machine. Telling that delivery speeds of up to 550 m/min are achieved with it today, he notes: “Due to the ring-spun yarn-like structure of air-spun yarns, the good automatability and the approx. 20-fold higher take-off speed compared to ring spinning, this spinning process promises a market potential of approx. 15 %.”
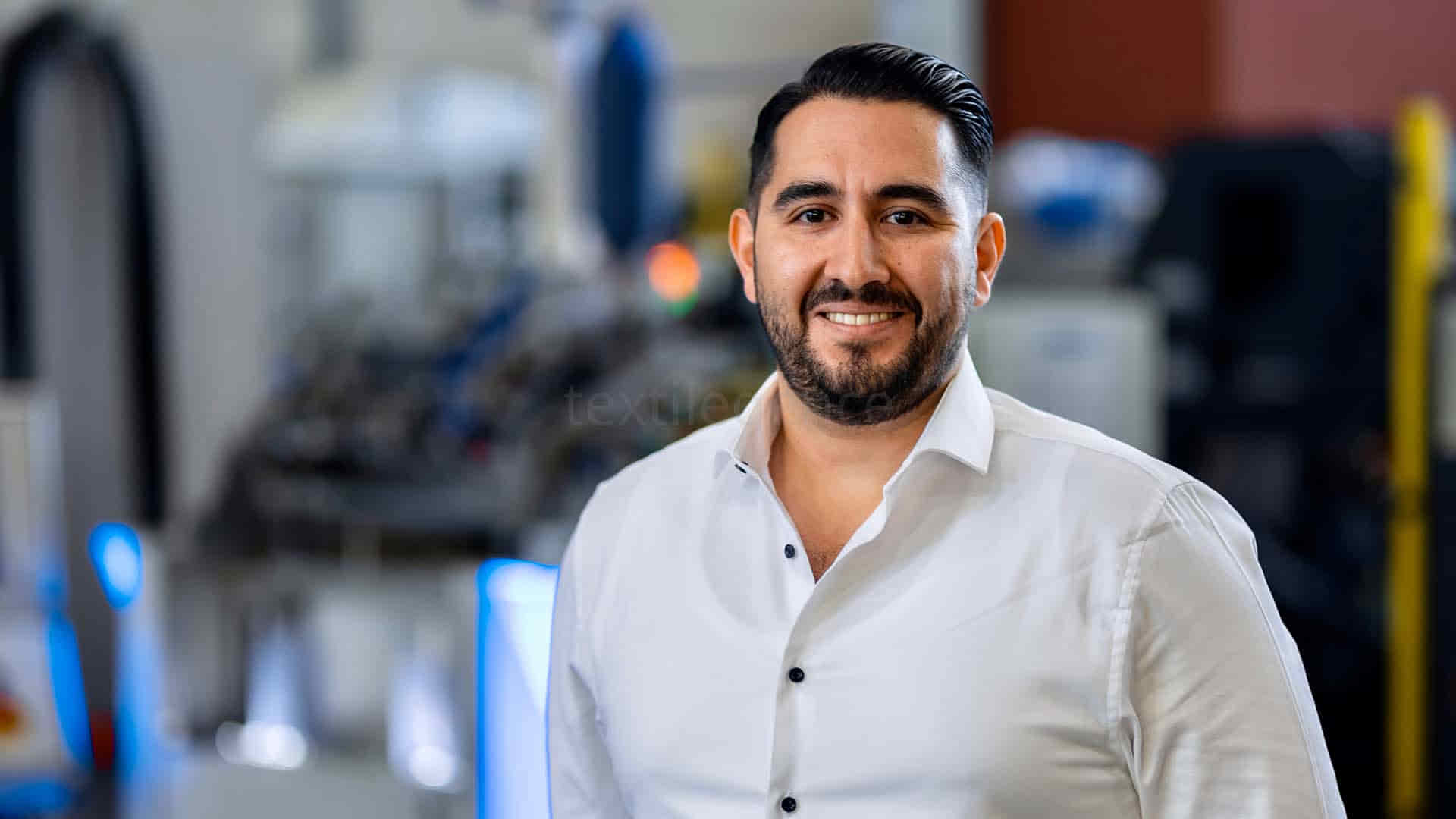
Halaç explains that high-draft systems do not differ much in their functions from the conventional drafting systems of spinning machines, but the main differences lie in the higher peripheral speeds of the roller pairs and in the option of higher drafting speeds. Saying that high drafting systems are therefore used to achieve production-economy goals in yarn manufacturing and are nowadays used in air spinning machines, he disclosed that for the currently common draw-off speeds of around 550 m/min, mainly 4over4 high drafting systems with a double apron unit in the main drafting zone are used.
“Fiber control in a high-draft system is essential to achieve high yarn qualities”
Research Associate Seyit Halaç notes that the uniformity of the spun yarn is directly related to the drafting quality of the sliver during the drafting process, however, due to aerodynamic challenges, the efficiency of the high-draft system is reduced. He discloses: “During the drafting of the sliver, drag flows form at the pair of output rolls, which flow out in the nip area both axially and in the opposite direction to the fiber transport direction (Figure 4). As a result of the transient airflow phenomena due to the high speeds of the pair of output rolls, the sliver is spread. This causes individual fibres to be deflected, which results in a high yarn non-uniformity due to thick and thin places. Therefore, adequate and controlled fiber control in a high-draft system is essential to achieve high yarn qualities.”
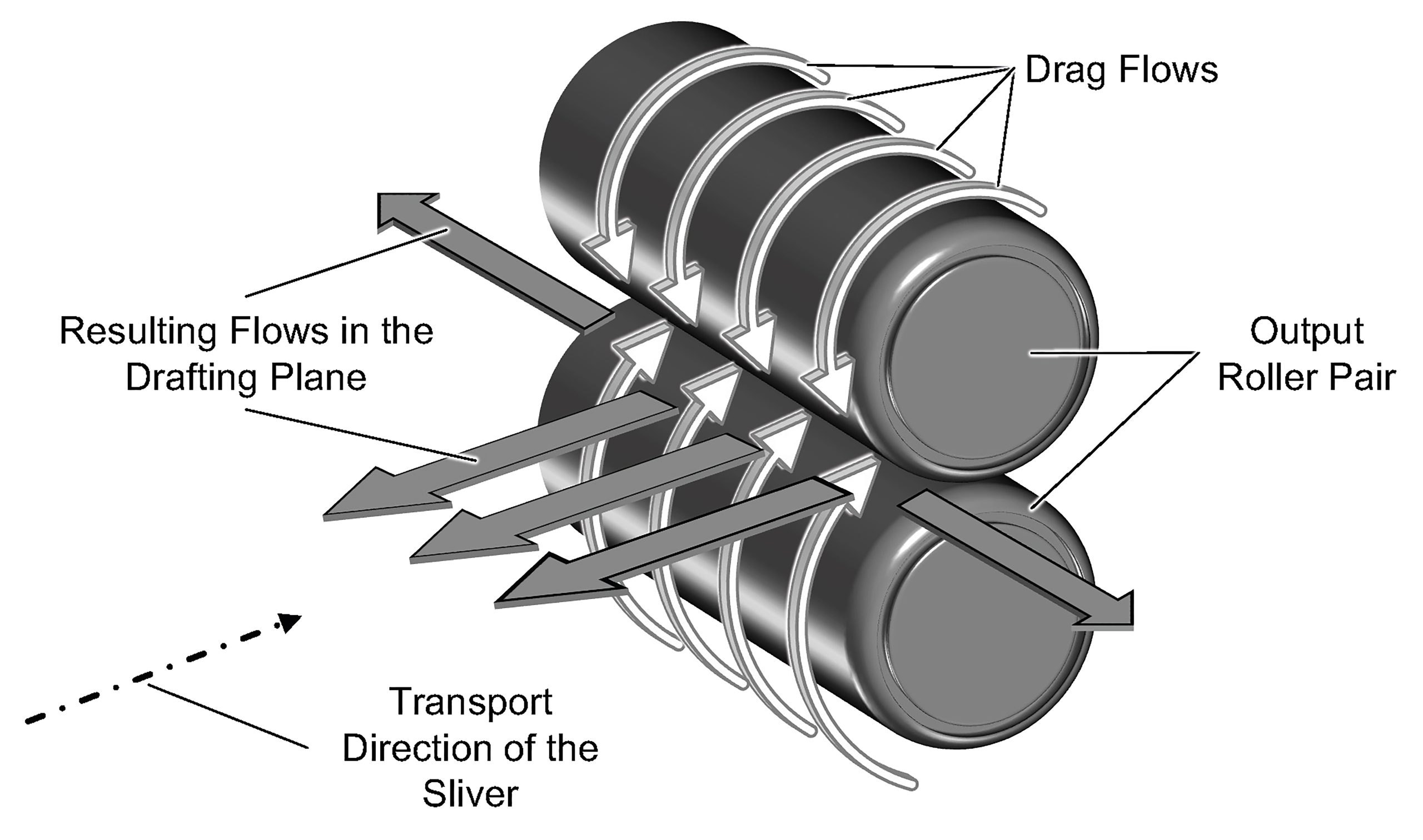
“The solution for the double apron’s disadvantages is a static fibre control element”
“To counteract uncontrolled fiber movement by breaking up the sliver into individual fibers, the fiber composite in the main drafting zone is conveyed to the output roller pair via a double apron unit. The aprons are usually made of synthetic, fiber-reinforced materials,” explains Research Associate Seyit Halaç, pointing out that a disadvantage of this application is the shortened service life of the aprons due to high surface wear caused by abrasive as well as thermal wear. He says that this results in additional maintenance costs due to production downtimes, in addition, impurities such as dirt particles and dust at the deflection points as well as the friction-locked apron drive can lead to jerky running (stick-slip effect), which disturbs fiber draft.
Halaç discloses that the mentioned disadvantages of the double apron drafting system can be compensated by substituting the double apron unit by a fixed fiber control unit: “In national as well as international disclosure and patent documents, unsteady airflow phenomena in the main drafting zone of drafting systems are mentioned as the cause of sliver unevenness. In the mentioned disclosures and patents, the detachment of the fibers from the fiber structure in the main drafting zone is solved by replacing the lower or upper apron with a static fiber control element.”
“Single-apron drafting system also provides energy saving”
Research Associate Seyit Halaç says that results for spinning preparation machines (e.g. roving frames) as well as for spinning machines (e.g. ring spinning machines) show that the single-apron drafting system improves both the uniformity and the strength of the drawn sliver. He continues; “These results are due to the reduced stick-slip effect between the upper apron and the lower fiber controlling element. Furthermore, the elimination of the bottom apron reduces energy requirements. Reduced maintenance, as well as reduced wear, are further advantages of a fixed fiber controlling element.” He added that by converting the double-apron drafting system into a single-apron drafting system, the technological and production-related disadvantages of the double-apron drafting system of an air-spinning machine can also be compensated.