Stratasys, recognized as one of the pioneers in 3D printing technologies, offers a comprehensive polymer portfolio, with various range of solutions available. The company presented the first version of the J850 TechStyle™ direct-to-textile 3D printer, which provides a new approach to the industry at ITMA 2023. J850 TechStyle printer appeals to a range of new fashion applications by bonding full-colour, translucent, rigid, and flexible materials directly onto textiles and garments.
Giving a special interview for Textilegence, Stratasys Ltd. Product Manager Ofer Libo expressed their excitement about participating in ITMA 2023 for the first time and evaluated the exhibition and the role of Stratasys as: “We know that the industry went into sort of a hibernation mode after the pandemic for the past four years, but now it is very nice to see everyone coming and indulging in new technologies and meeting up with each other. We are the biggest company in the world that develops, manufactures, and sells 3D printers. We are leading the AM (Additive Manufacturing) industry, and as part of that industry we play in various applications, and different segments such as automotive, aerospace, medical, prototyping, and product development. In the past couple of years, we started to venture into the textile and the fashion industries.”
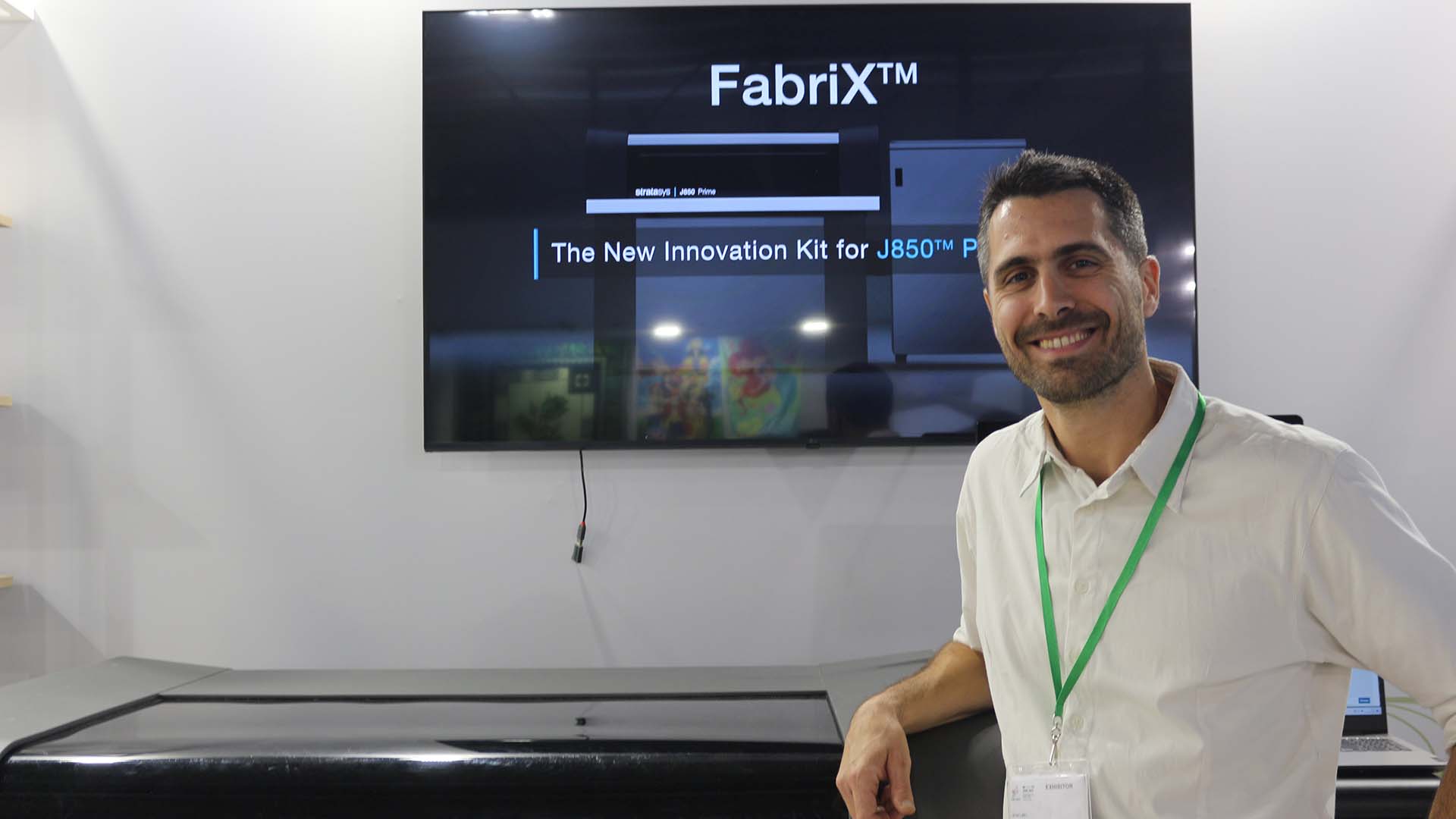
Stratasys showcasing J850 TechStyle printer powered by 3DFashion™ technology
Addressing Stratasys’s concept and new developments, Ofer Libo stated that their core technologies are now being applied directly to textiles. Libo noted that the Polyjet technology has been around for more than 30 years, moreover, it is one of the oldest and most reliable 3D printing technologies. He detailed the developments of this technology: “We started to play with this technology and apply it to fabrics and textiles. In the last few years, we went into development mode to get a product into the market. Last year during the Milan Design Week, we launched the first version of the J850 TechStyle printer, which is powered by 3DFashion technology.”
It is highlighted that the J850 TechStyle printer supports the textile manufacturers working for upscale fashion labels and designers in crucial industries like automotive and haute couture by providing them with unlimited design possibilities as well as flexibility. Libo explained the new developments and their contribution to the industry: “Originally, 3DFashion technology or the J850 TechStyle printer was designed for production. So, the operator will feed sheets of textile or fabric into the machine, and we will print on them. Then the designer will take it and cut and sew the printed fabrics into the final product, creating the finished good. With the Direct-to-Garment tool that we are going to release soon, we want to enable our customers to print directly on the garment. For example, if you have a jacket, you can just place it straight onto the machine, onto the specific tool, and then press print, meaning you could modify or give second life to garments, to what you wear now basically.”
Libo also noted that besides the J850 TechStyle printer, they have another incoming innovation for the transformation of the industry. He disclosed: “We are working on a new software tool to help the designers transform 2D images to 3D objects quite easily. We understand there is a gap between designers or industrial designers, who develop their products in 3D, and fashion designers who are used to 2D images. That’s why we want to make sure that we enable them to have a smoother path from 2D to 3D. We will announce the developments in the future.”
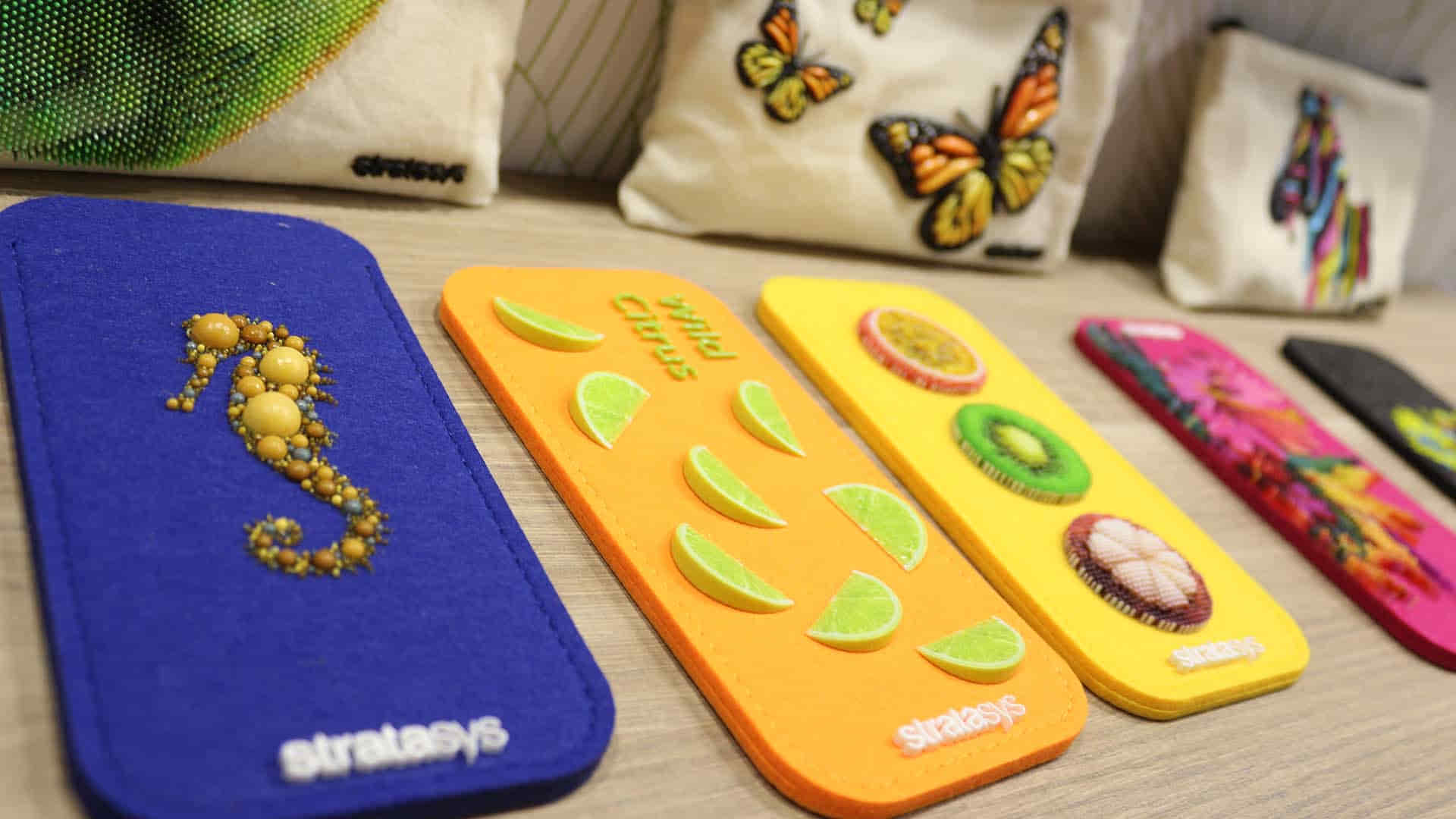
“We see huge potential to implement digitalized processes into the textile industry”
Ofer Libo asserted that 3D printing could affect the textile industry in many ways. He also emphasized that the textile industry is very traditional, very old-fashioned in terms of processes and adoption of new technologies and continued: “As people are coming from the 3D printing, from the AM industry, we see huge potential to implement digitalized processes into the textile industry. 3D printing could influence fields such as the creation of accessories for end-use parts for the actual consumers, such as customized accessories with different materials, or even machine parts for the production floors. Just imagine that you have something broken down in your machine. In that case, you get stuck, so you quickly go to your 3D printer, design the part that you are missing, print and install it.”
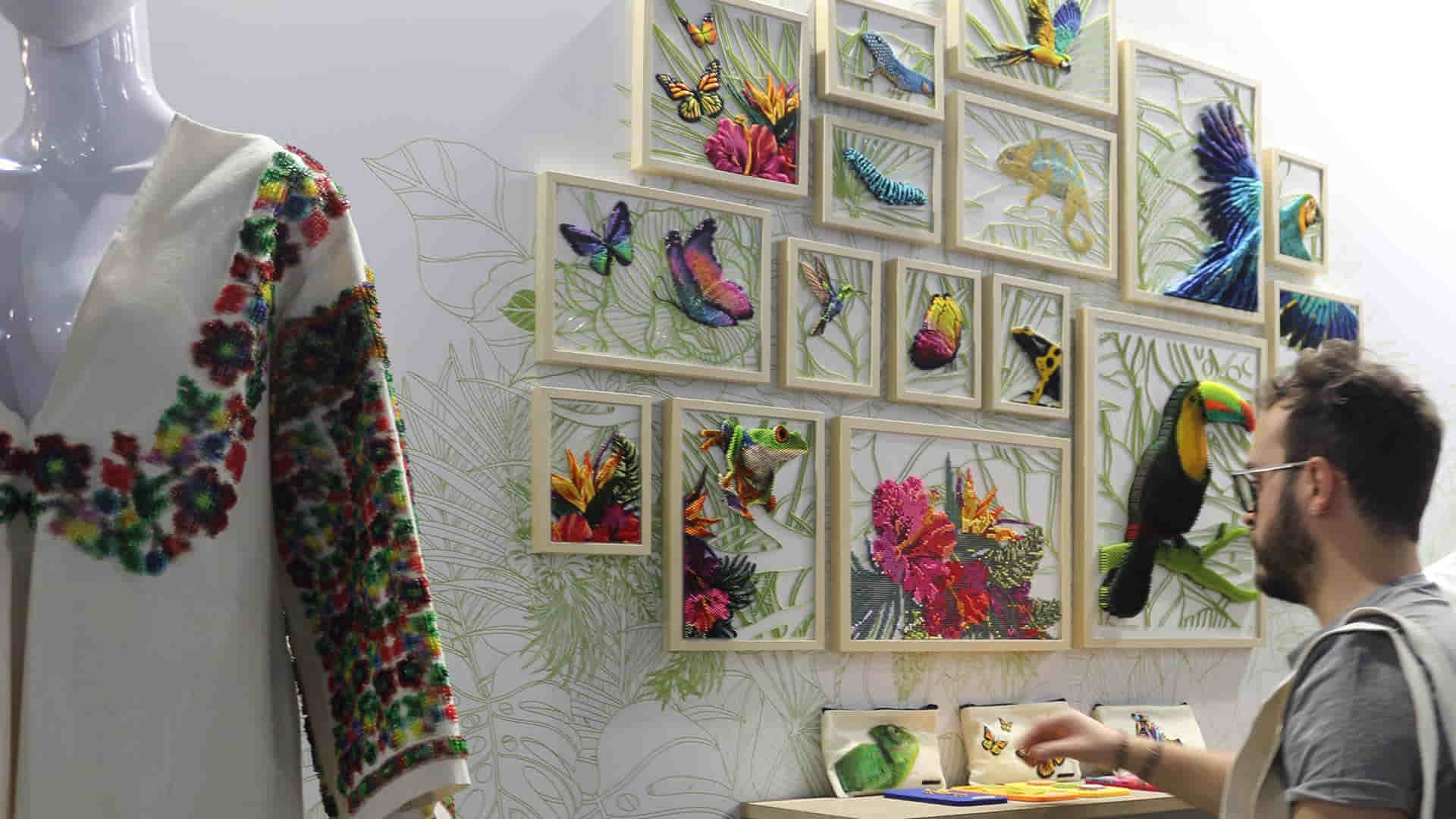
“Turkish textile industry has a huge potential for 3D printing”
Welcoming visitors all over the world, Ofer Libo noted that Stratasys’ booth has also been visited by numerous Turkish customers. Libo evaluated the Turkish market concerning the textile industry and 3D printing: “I know that the textile market in Türkiye is very developed. There are a lot of different brands that are producing, designing, and manufacturing in Türkiye, whether it is for the fashion industry or the automotive industry, which is also a very important player and segment for us. We are looking for new opportunities we definitely think there is a huge potential for that as well.”