Textile technology manufacturer, Monforts is the only company that can offer a complete range of coatings from a single source today and introduced the latest Montex Coat magnetic roller coating option to virtual delegates from all around the world at the first edition of World Congress on Textile Coating organised by International Newsletters. Monforts Head of Technical Textiles Jürgen Hanel took part as a speaker at the conference held on February 11, 12, 18, and 19 and he explained the features of magnetic roller technology and what it means for the textile world.
Monforts’ magnetic roller coating technology especially is accepted by technical textiles and nonwoven fabric manufacturers. Typical applications for Montex Coat include the finishing of tents and awnings, black-out roller blinds and sail cloth, automotive interior fabrics and medical disposables. Full PVC coatings, pigment dyeing or minimal application surface and low penetration treatments can all be applied.
In his speech at the first edition of World Congress on Textile Coating, Monforts Head Of Technical Textiles Jürgen Hanel told the importance of flexibility, product uniformity and automation, and emphasized that these are the keys to success for coating businesses in today’s rapidly-changing technical textiles industry. Stating that the digital event really reflects the positive changes in the textile industry, Hanel continued his words as follows; “I look forward to the next edition, which hopefully will be a face-to-face event for even deeper level discussions and debate”.
It offers textile finishers a wide range of options
Jürgen Hanel emphasised that the magnetic roller system is easy to handle for operators, while also making it possible to be carried out a wide range of coating and finishing operations. Hanel said; “It is much easier to clean at the end of the process. It provides textile finishers with an expanded range of options due to the fully-adjustable positioning of the magnet within the roller and with four different magnet positions possible. It can be set to operate both as a direct coating system and as an indirect coater”.
Consistent results even at wide widths with Montex Coat magnetic roller
With traditional dip coating systems, as well as with many standard knife coating technologies, there is always a difference in the tension between the center and edges of the wide width fabrics being treated, and hence the amount of pressure with which the coating is applied. With a magnetic roller, consistent results can be achieved even at wide widths of over 2.4 metres by applying equal pressure across the full width of the fabric. In addition, adjusting the roller surface, rather than changing the coating formulation to match the required add-on and viscosity for each coating effect required, leads to much higher productivity from the line.
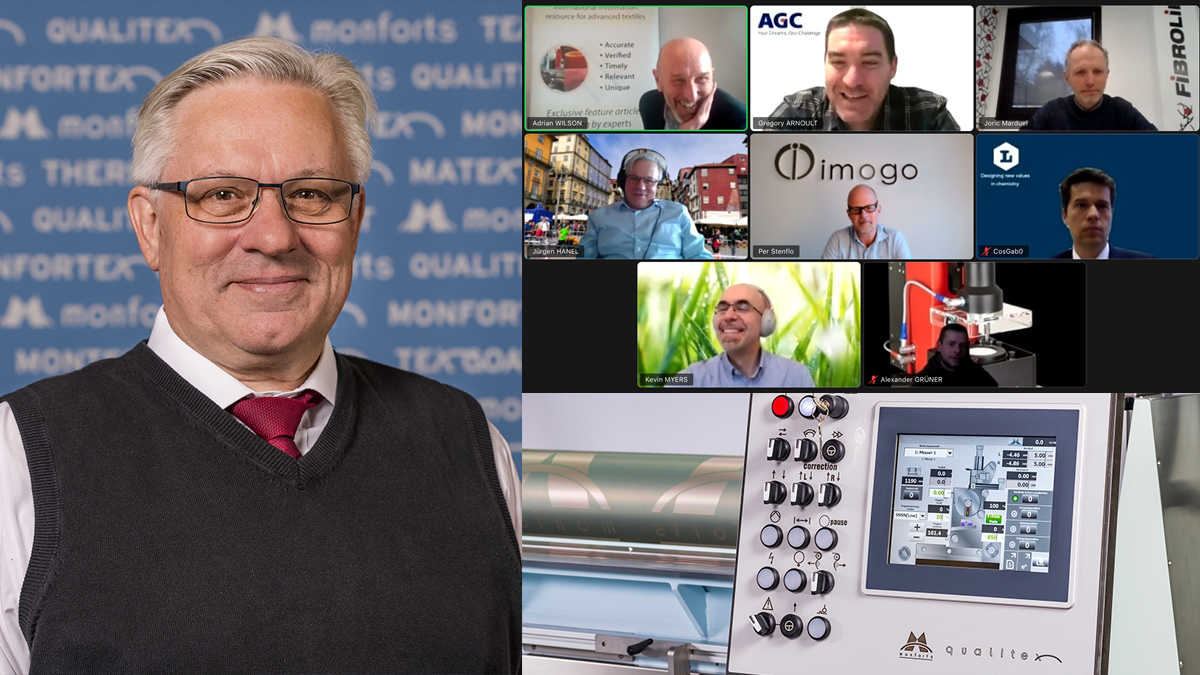
Automated coating line ensures 100% reproducibility
Stating that a typical integrated Monforts coating line is automated from the inlet feed to the winder, Jürgen Hanel commented; “Adjustments can also be made simply and easily from the touchscreen and with the new hand-held remote controller which has recently been introduced for the Montex Coat unit”.
Manual adjustment takes a lot of time, as well as requires the attention of an experienced operator. Otherwise, reproducibility between coating operations is not certain. The adjustment by motors allows each coating to be stored and downloaded again for 100% reproducibility. While the motors can be fully controlled from the touchscreen, all necessary adjustments can be carried out remotely. In this way, switching between processes becomes extremely quick and easy.
Today’s most exacting customers demand accuracy, especially when dealing with the winding tension required in the processing of materials such as prepregs for composites and other heavyweight fabrics. Customers’ requirement is met thanks to the optional carbon fibre roller.