Baldwin Technology Company Inc. has announced that corrugated packaging market leader VPK Group has recently installed a FlexoCleanerBrush. This new system, which automatically cleans and dries corrugated printing plates in less than four minutes, has been added to VPK’s advanced 2.1-meter-wide six-color Göpfert Ovation High Board Line flexographic printer at the company’s new high-bay factory in Halden, Norway.
Robert Stade, Project and Technical Manager of VPK Group said that they are excited about the advanced cleaning automation now enabled at their new plant. Disclosing that besides not having to stop production for manual cleaning, Stadesaid that now they can regularly have multiple plates cleaned more efficiently, both during and between print runs. Stade; “As a result, we have increased our production capacity and dramatically decreased our downtime”.
VPK Group confirms the advantages of automatic cleaning
VPK Group offers customers sustainable and innovative corrugated solutions. For the new plant, an independent study was conducted to validate the capacity of Baldwin’s FlexoCleanerBrush system. The study measured all performance data and validated that the automated system could fully clean and dry all printing plates in less than four minutes and pick hickeys in seconds.
Lee Simmonds, Regional Sales Manager at Baldwin said; “The FlexoCleanerBrush is truly an innovation for post-print flexographic printing onto corrugated boards—there is nothing even remotely comparable on the market”. Simmonds continued his words as follows; “Thanks to the elimination of micro-stops mid-run to clean plates, print jobs are set up faster from print run to print run, and as a result, the system reduces lost hours over a week to just minutes. Further, the high print quality is maintained and even further enhanced”.
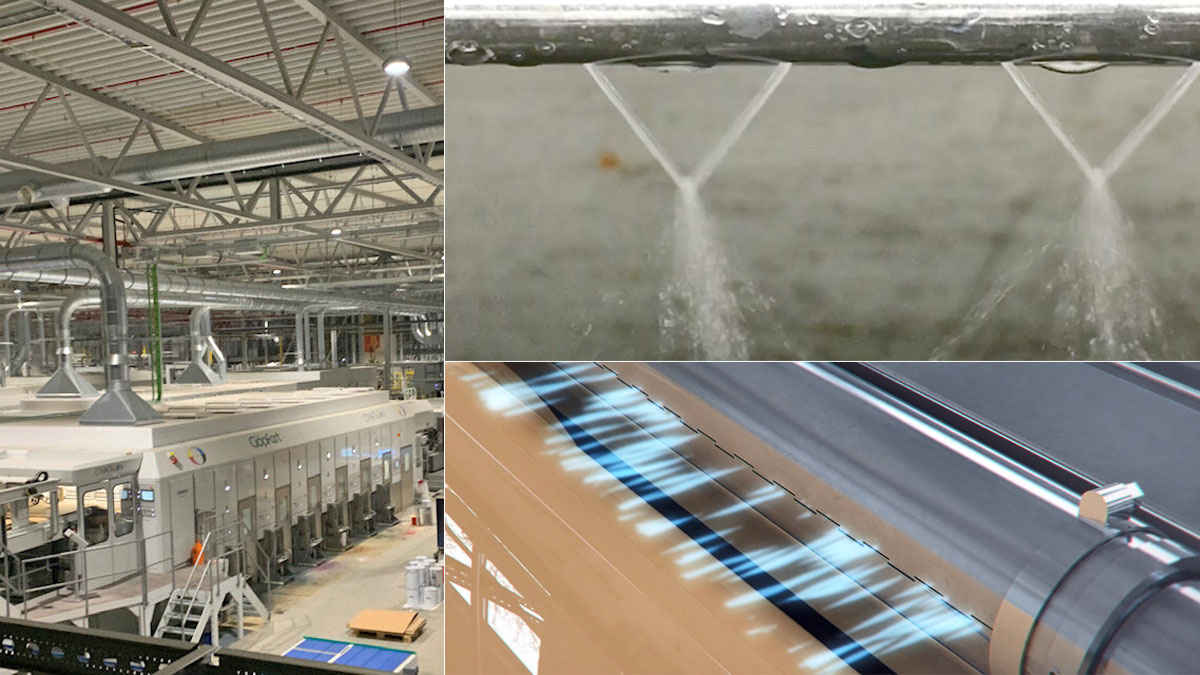
Automatic cleaning capacity in seconds
With the FlexoCleanerBrush system, an inline cleaning station installed within each print unit uses a brush; that runs the full width of each printing plate. Paired with a precision spray application system; the FlexoCleanerBrush evenly distributes a mixture of approximately five percent detergent and water across the plate as it spins; gently cleaning its surface. The plates are then dried by the integrated air knife. Cleaning cycles can be controlled through the FlexoCleanerBrush’s operator panel or the integrated Göpfert human-machine interface.
Besides offering efficient cleaning during runs and fast end-of-job cleaning; the FlexoCleanerBrush system also enables operators to remove dry plates from the machine; without the potential risk of plates sticking together once they are placed back in the plate-racking system. This helps to ensure increased board throughput, less downtime and a safer working environment; by eliminating operators’ contact with nip points, moving parts and chemicals.