Yarn manufacturers focus on maintaining their quality and efficiency high, at the same time, lowering their operating costs in the market conditions where fierce competition is taking place. The difficulties of working with contaminated cotton increase the costs in this process. Asteks has recently introduced its new generation draw frame cots, which are successful in the face of contamination that is specially case with the local cottons. E-750 / HG-650; A new generation of Asteks’ draw frame cots, HG-650 finisher drawing frame cots and HG-650 combing frame detaching roller cots have succeeded to become one of the most important component for spinners, in short time.
Asteks HG-650, 65 shore draw frame cots, has period of clean stay by 50% longer than compared to similar ones. In field studies, it was observed that this cot needed to be cleaned once in every 2 shifts. HG-650 also has a longer grinding period. Asteks has confirmed that grinding every 60 days is sufficient for efficient work by their field study. With similar products, the grinding requirement is seen as half of this, which means that the life-time of cots is equally lower. These data, compiled by Asteks under real production conditions in the market, differ according to the processes in the mills and the cotton used, but remain at better levels than the similar ones to them.
Another superiority of the new generation cots can be seen in the sliver quality data with better USTER unevenness values. The Asteks HG-650 combing machine drafting cots also provide positive results in terms of USTER quality values compared to other brands as well as the advantage of the easy run against lapping.
Asteks manufactures innovative and functional products
Sabri İlknur, Asteks Marketing and Sales Manager, said that they have started to produce innovative and functional products due to the increasing machine speeds and increasing fibre diversity in recent years. İlknur continued his words as follows; “Achieving and increasing fibre control in the spinning processes are of high importance for both yarn quality and cost management. Draw – Combing frame cots, those we offer, provide spinners the solutions what they are looking for. These cots with late contamination feature, fulfil important tasks in securing the quality and efficiency at following processes enabling fibre control and transfer, better. Customer feedback about the increase in mill efficiency, savings and production quality makes us very happy”.
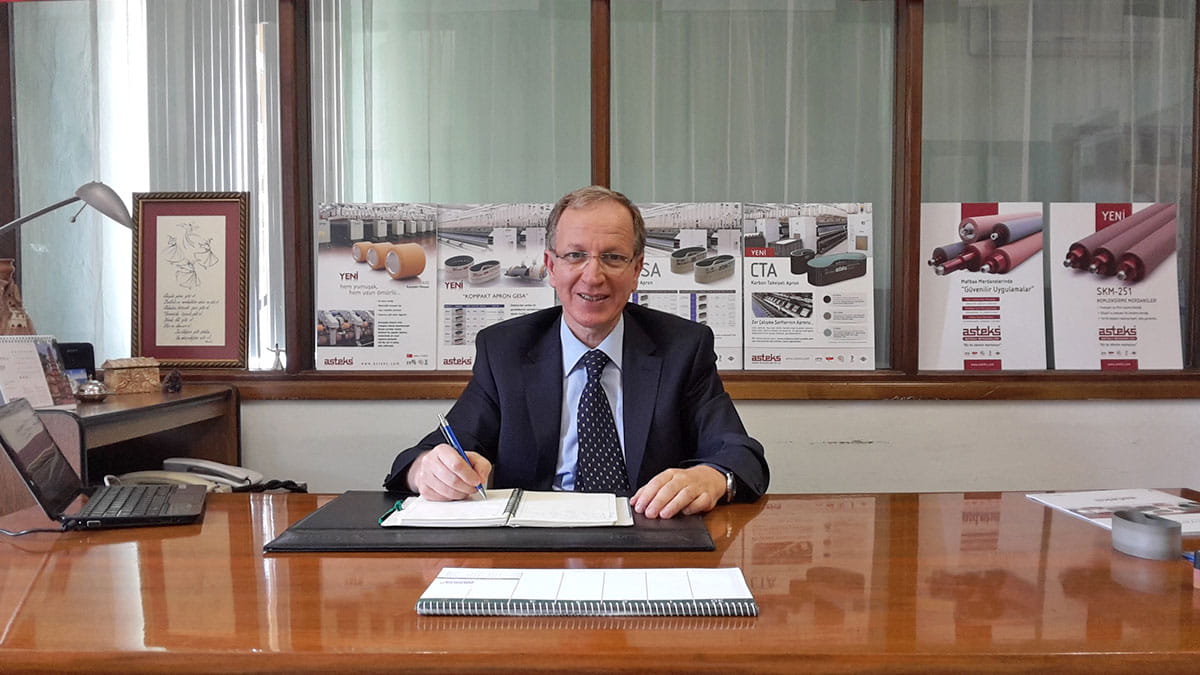
Bülent Topal, Mariteks Spinning Factory/ Kahramanmaraş Operation Manager:
We have been using Asteks’s new draw frame cots for eight months and we are very satisfied with their performance. Our cleaning periods, which had been hardly long as per a shift, only, with the original sleeves that came with the machines, were easily extended up to one day with Asteks’s HG-650 draw frame cots.
When processing contaminated cotton, it is the best to clean the cots at the beginning of every shift, but the HG-650 can continue working throughout the day without being wiped. We have experienced that HG-650 draw frame cots had not required grinding in longer than 2 months, under the normal working conditions. We did not record any loss in our yarn quality and USTER values in this eight months running time. In great relief, I use Asteks’s new draw frame cots without any concern about yarn quality values”
In addition to the high quality of the product, it is very important for us to be supplied quickly. While it can take 4-5 weeks to bring cots from abroad, Asteks’s cots are delivered in 1-2 weeks upon our request. It also has a better economic advantage of 20-30% compared to other known brands on a cost & benefit basis. Our cooperation with Asteks continues in stronger relation provided by such this high quality production and successful services.
Hüseyin Güler, Gülle Tekstil Technical & Maintenance Coordinator:
Asteks’s HG-650 draw frame cots are getting dirty 15-20% later compared with its competitors. Of course, the rate of contamination in cotton can shift this time up or down. As Gülle Tekstil, we clean the cots in each shift. However, this particular cots are able to complete their work in entire shift without cleaning required. As a textile company, the frequency of grinding is important to us. Providing much better values in draw frames, HG-650 is a much better product compared to similar ones to it, in terms of both maintaining cleanliness and quality.
In addition, the HG-650, which we use on the ring compact spinning machine, can maintain its good quality performance without grinding between 30 to 45 days without disrupting the yarn quality. We achieve USTER quality values, yarn imperfection values, such as thin place and thick place, much better than other cots that I have bought from Europe.
When we have a cots requirement, Asteks can send us in three days; if I request this from a European manufacturers, the product does not arrive before 3 months. This is a huge advantage for us. We do not have obligations such as suspending the production; due to shortage of the cots and keeping high cots stock. The product and service quality of Asteks, who works as a partner with the textile industry and conducts R&D studies, is higher than its European competitors and in this sense I find Asteks very successful.
Metin Özdemir, Rubenis İplik Factory Manager:
As Rubenis İplik, we try to implement high quality oriented and extra careful production processes. We clean the draw frame cots every hour in the shift. We apply more cleaning than a standard yarn manufacturer does. We grind the HG-650; which have a longer time sustainability in keeping itself clean than other competitive products; every 15 days due to our high sensitivity in production processes. We can easily further extend the grinding time, but we keep it short for our special yarns.
The period of staying clean and grinding we obtained with the HG-650 draw frame cots is much more positive for us. As the HG-650 is sustained cleaner by its own nature; thin places, thick places are reduced in the further processes by these good quality slivers. Compared to the conventional draw frame cots, we achieve remarkably better yarn quality values with the HG-650 draw frame cots. We clearly saw this with USTER quality test results. I would like to state that we especially prefer Asteks in terms of cots quality.
Tarık Karagözoğlu, Texhong Textile Machinery & Energy Responsible:
Our factory has been operating for a year; and we have been using Asteks’s HG-650 draw frame cots for 5-6 months. In our studies, we have observed that these cots remained clean longer than other brands. HG-650 cots are 30% better than other similar ones to them in terms of late contamination.
In every shift, we apply cleaning to the draw frame cots twice as standard. The quality is the most important factor for us; and we apply the grinding every two weeks in order to keep our yarn quality away from the smallest risk in this respect. We observed improvements in yarn imperfection and other quality values; while using the HG-650 draw frame that can work suitable with all machine brands and models. As Texhong, as we are quality oriented; we preferred Asteks’ HG-650 draw frame cots, which contributes to customer satisfaction and production efficiency.