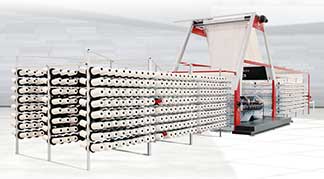
High-tech circular weaving receives an upgrade: Based on the RX 8.0, Starlinger launches the RX 8.0 II with several new features. Version II scores with an optimized shuttle and reed design in combination with the most modern electronic components for energy-saving operation and easy handling.
Since 2013, the circular loom RX 8.0 for high-strength tape fabric has been convincing customers all over the globe; with excellent fabric quality at low production costs. To increase the efficiency of the RX 8.0 even further, it was revised in 2018 and presented as the RX 8.0 II in the Starlinger factory in Taicang/China. In addition to the optimized 8-shuttle-design, the machine now possesses an improved and extended reed with 2400 instead of the previous 2160 positions.
The RX 8.0 II operates at a production speed of 800 picks/minute with a double flat working width of 1700 – 2250 mm. The energy-saving motors are equipped with frequency converters; the circular loom is controlled via smartTRONIC on the intuitive 7” color display. Operators will also appreciate the significantly reduced noise level of the machine.
Plastic fabrics for heavy-duty applications
“The outstanding production efficiency of Starlinger circular looms results from low operating costs paired with a high IQ;” explains Starlinger Sales Director Hermann Adrigan (Note: IQ stands for Indicator of Quality – the average woven fabric meters produced without warp breaks). “In October, the first RX 8.0 II circular looms were delivered to a customer in Southeast Asia; who produces plastic fabrics for flexible intermediate bulk containers (FIBCs). Thanks to the completely oil-free weaving process, the produced fabric is also suitable for packaging food products such as seeds.”
High-strength fabrics are used in a variety of heavy-duty applications; FIBCs for transporting large product quantities, geotextiles for landscaping, agrotextiles for agriculture; tarpaulins for protection against wind and weather. The material is manufactured on circular looms which process PP, HDPE, or PET tapes into robust fabric. The technology behind Starlinger circular looms is certainly impressive: Mechanical components are constantly optimized and complemented with state-of-the-art electronics. The focus lies on high fabric quality, cost-efficient production, low maintenance, and easy handling.