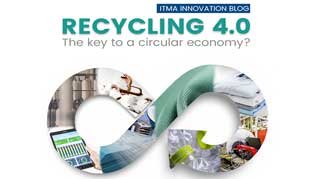
Technologies which can greatly assist fabric manufacturers in saving or recycling resources have become increasingly important at successive ITMA shows. This is especially the case in the area of fabric finishing, where huge volumes of water, steam, chemicals and thermal energy have conventionally been required.
The leading manufacturers of finishing technology have been addressing this through concepts such as alternating and split-flow air circulating systems within their dryers, to ensure the optimum temperature distribution, assisted by integrated heat recovery systems which are now becoming standard.
A further portion of these resources, however, can be wasted without precise feeding, monitoring and control, and there is now a move away from the conventional dipping or padding processes in which fabrics are submerged into liquid coatings, to systems that can apply finishes onto fabrics more sparingly, and increasingly only where they are required.
This not only saves on the amount of chemicals required, but also ensures the energy needed for the subsequent fabric drying process can be dramatically reduced. Such technological developments alone, however, will not come close to being enough to move the textiles and clothing industry towards becoming part of a future circular economy.
Recycling and integrated supply chains
A much more co-ordinated, industry-wide approach is being demanded, and Industry 4.0 is promising to enable it.
At the last ITMA exhibition in Milan in November 2015, I was particularly struck by the observations of Zhang Jie, chairman of China Hi-Tech Group Corp. He observed that his company’s focus was on the synchronisation of all of its operations, having then just installed its first intelligent spinning factory in China that could be fully controlled by mobile phone from anywhere in the world. Given the pace of change, such plants are rapidly becoming standard.
“Increased automation and digital control will be accelerated across all of our machine ranges and this is only the first step,” Zhang Jie said. “We anticipate the further full integration with both suppliers and customers, because completely integrated supply chains are the future.”
Completely integrated supply chains surely hold the key to how to address the fact that 73% of the world’s clothing eventually ends up in landfills or is incinerated, or that currently less than 1% of the material used to produce clothing is recycled into new clothing.
Only Industry 4.0 – and the sort of fully integrated supply chains Zhang Jie spoke about – could enable this, but the gains could be simply enormous.
If today’s textile collection rate tripled by 2030…
According to the Ellen MacArthur Foundation, if today’s textile collection rate tripled by 2030; it would be worth more than €4 billion to the world economy.
This figure, however, merely represents the value of those products that would not end up in landfills. If the industry were to somehow find a way to collect and recycle all of the fibres it processes – over 100 million tons annually –; it would boost the value to over €80 billion. There is currently terrific work going on in this area.
The Refibra project, driven by cellulosic fibres producer Lenzing, for example; teaming up with Spain’s Inditex and Zara as one of the world’s biggest fashion groups; is taking the closed loop manufacturing of regenerated fibres to a whole new level.
Establishing the Refibra programme has involved collaboration across what is currently a very fragmented textile value chain; and has called for significant collaboration and transparency at an unprecedented level. This is paramount for establishing efficient recycling chains and Industry 4.0 can move them one stage further.
Software companies
In another interesting and related development; German warp knitting technology leader Karl Mayer has recently joined ADAMOS – ADAptive Manufacturing Open Solutions –; an alliance of technology companies with combined annual sales of over €20 billion; and very big ambitions in terms of Industry 4.0.
ADAMOS is intent on bringing the machinery and software industries together; focusing on the industrial machine sector and developing industry-specific Internet of Things standards; and shared services across a wide ecosystem.
“As such, it is lowering the entry barriers to manufacturing companies everywhere; reducing risk and allowing for experimentation using state-of-the-art technologies,” says Eric Duffaut; chief customer officer of founding partner Software AG. “It allows for every manufacturing company to accelerate its transformation into a software company; no matter what size.”
It is this transformation at a company level; along with the move towards completely integrated supply chains; that will make the eventual collection; and recycling of all of the fibres involved in the €3 trillion+ global clothing industry; much more than a pipe dream.
And all of the technologies that are powering it at ground level will be on display; and demonstrated at ITMA 2019 in Barcelona.
Writer: Adrian Wilson
Source : Link